Wear? Where?
The reports generated by an oil analysis program have a lot in common with a complex jigsaw puzzle. As important as the individual pieces may be, their real value is found in the way they fit into the bigger picture.
“Typically you don’t see just one wear metal,” explains Dan Arcy, OEM technical manager for Shell. Each reading needs to be considered in the context of other data before it will identify the true nature of a problem. A technician who spots an increase in copper might immediately assume that the metal has come from a disintegrating bearing.
But not so fast. Caterpillar engines use aluminum in their bearings. The individual reading also might be traced to a new oil cooler before a process known as passivation begins to create a protective coating around the copper tubes.
When the wear metal actually is coming from a disintegrating bearing, it likely will be accompanied by increases in tin and lead.
It is not only the individual piece of data that can lead a technician astray. Spikes in silicon often will lead maintenance teams to suspect there are abrasive particles of dirt in the oil, but when that is the case there also will be higher readings of calcium or aluminum, adds Mark Minges, the chief operating officer for Polaris Laboratories.
When those metals appear, it may be time to investigate the engine’s air filter as well as the related clamps and connections. If the silicon appears on its own — and without any increase in wear metals — the dirt actually may have been picked up during the sampling process itself. All it takes is someone who waits too long to put the lid on the sample bottle.
The silicon might even come from something else entirely. At least one engine manufacturer uses a bead of silicone to seal its gear case cover, notes Lilo Hurtado, an application engineer with ExxonMobil. In this case, the silicon gradually will disappear over the course of three or four oil drain intervals.
Of course, dirt is not the only source of abrasive particles that can wreak havoc on engine components. Soot also can begin to increase in the wake of a failing exhaust gas recirculation valve, restricted exhaust or “blow-by” that forces fuel, air and moisture past the piston rings.
That material’s abrasive power is bound to lead to higher levels of iron, chrome, nickel and aluminum from the upper end of the engine, Minges says.
But as important as the readings of different metals can be, Hurtado stresses one of the most important readings of all will come in the form of the oil’s overall viscosity. “As long as you can maintain the viscosity of the oil, you know you are allowing it to perform its lubricating function,” he says, noting how the protective coating can be affected by a number of factors.
Oil certainly will thicken if it is exposed to unwanted coolant, which can be spotted by the spikes of potassium and sodium in an analysis report, notes Vic Kersey, Valvoline’s technology director – commercial products. “Some engines are more prone to leakage than others.”
Once that happens, the chemicals will begin their attack on the overlays on bearings and bronze bushings. Over time, the oil will form a peanut-butter-like sludge that actually plugs oil galleys, leading to the threat of a catastrophic engine failure.
Like everything else, the chemicals that might suggest a coolant leak also can be caused by another factor. Hurtado, for example, explains that some technicians who discovered higher levels of potassium and aluminum in their oil samples discovered that the material could be traced to the brazing flux being purged from charge air coolers.
It was more common during the early days of exhaust gas recirculation, but Hurtado is still seeing it. “There’s a lot of surface area on there, and there’s a lot of brazing that takes place,” he says.
Coolant is not the only fluid to have an impact on the oil’s viscosity, either. High levels of fuel, for example, can thin out the fluid so it can’t form a protective coating around metal components.
Small amounts of diesel in the crankcase will tend to “boil off” before any problems emerge, but the issue may present a bigger challenge for those who are using biodiesel, Hurtado notes. Unlike a petroleum-based diesel, this fuel has a boiling point very similar to the oil itself. It isn’t going to go away.
Then again, a different viscosity is sometimes due to something as obvious as a different weight of oil. A shop may not be accounting for the fact that a sample is drawn from a new engine fresh from the factory. The manufacturer may deliver a wet engine with a supply of 10W30 oil rather than the 15W40 formula that is the standard lubricant in the rest of the fleet.
Look deeper into the formulas themselves, and there even can be differences in the chemical make-up between one chemical and the next. When levels of molybdenum (“moly”) push over 10 ppm, technicians might immediately think there is a threat to the piston rings, but those who use Shell’s Rotella T3 oil will need to watch for an increase that builds on top of the 50 ppm of moly that is used as an antioxidant.
If there is a lesson to be learned from all of the differences, it’s that labs rely on accurate information in every field of an oil sample’s label. Technicians need the facts about the make, model and year of an engine, along with the exact mileage on the odometer and details about the oils that have been used.
Arcy says, acceptable limits for iron, copper and lead will vary from one nameplate to the next.
It is why Kersey is wary if a shop claims the oil has been in service for 20,000 miles. “They must be guessing because nobody has exactly ‘two’ and four zeros.”
The metal make-up of each engine will vary among nameplates and specific models, Hurtado adds. “All of them are going to have their own fingerprints.” When generating any recommendations, a lab will draw on databases that account for differences such as some additional plating on the valves, or a difference in the chrome used to produce a crankshaft.
Even the size of the engine’s sump will make a difference in the reports. A lab may not be very concerned about a 150 ppm load of iron that comes from an eight-gallon reservoir, but the alarms will begin to sound if the sample has been drawn from the 89 gallon supply in a Caterpillar 3516-powered haul truck, Minges adds.
The more detailed the information can be, the better. “The less information we have, the more generic the interpretation is going to be,” he says.
While a shop is hardly as sterile as a laboratory, the samples themselves also need to be as clean as possible. In many cases, the quality of the sample will be dictated by the way the oil is extracted from the engine. “You can’t just drop a drain plug and take a sample,” Minges says.
Most labs prefer fluids that are pulled from an engine fitting that is installed upstream of the filter, and used while the engine is running and the oil is mixing. If the oil is pulled from the dipstick tube, the tool used to extract the sample should be suspended in the oil rather than pushed all the way to the bottom where any sludge can accumulate.
And those technicians who insist on pulling samples from the drain plug itself should take the time to let the engine warm up, and then let the oil drain for 15 to 20 seconds before filling the bottle.
The same process also should be repeated from one sample to the next. It is easier to trust emerging trends if the oil always is collected and measured the same way.
Then it is a matter of quickly closing the lid. It sounds like a simple step, but a surprising number of false readings come from debris on a lid or dust in the shop air. “Don’t take the lid off the sample jar until you’re ready,” Minges adds.
Indeed, the potential contaminants are everywhere, and they can make a real difference in the final reading. A few drops of a technician’s sweat might lead to the spikes in sodium that will lead a shop to think it is dealing with a coolant leak.
Kersey even has seen cases where someone has used an old antifreeze bottle to take a sample before transferring the oil to a proper sample jar. Then they wonder why there is a spike in the readings that normally are linked to a coolant.
Once the samples are in hand, they should be shipped to a lab as soon as possible, rather than waiting for days to pass, Arcy adds. “It’s catching something early that saves you from catastrophic failures.”
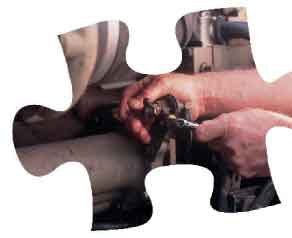
Of course the labs should be following some procedures of their own, and there are a number of questions that a maintenance team can ask when deciding who should inspect the samples. Some facilities are quick to cite quality control standards such as an ISO 17025 accreditation, but which tests are covered by the accreditation? And how are those who conduct the tests actually trained? Are they certified by the Society of Tribologists and Lubrication Engineers or does the lab train its employees to another standard?
Hurtado stresses the value of a simple tour of the lab, to see if the employees are thoroughly mixing samples with a mechanical shaker or simply reaching for a bottle that sits on the lab bench.
The final reports may offer one of the biggest differentiators of all. Some suppliers will incorporate the simple colors of a stop light to identify readings that are a cause of concern. Other detailed management reports allow fleets to mine the data, helping to identify the issues that might be linked to a specific maintenance facility.
Many companies will even feed data directly into computer maintenance management software systems, or give customers the chance to pre-register equipment so simple labeling errors are minimized. A shop, meanwhile, might want to focus on the style of report that will generate clear maintenance recommendations.
Above all, anyone who uses an oil analysis program should take the time to consider the potential return on the investment. Returns of 10:1 or 15:1 are typical once customers consider the maintenance savings from extended-drain intervals or reduced component failures, Polaris has found. It is the type of information that can secure a customer and establish long-lasting support for a program.
There is a lot of information that can be collected, so those who turn to the programs should take the time to decide exactly what they hope to accomplish, Hurtado adds. If the main focus is to extend oil drain intervals, the reports might need to hone in on oil oxidation and viscosity.
If the goal is to reduce premature component wear, the samples will need to be tested for coolant, fuel, viscosity and the contaminant and wear metals themselves.
This is all about looking for the missing pieces that will help to develop a bigger picture.
“There is a cost,” Arcy says of the programs, “but the payback is very huge.”