Chances are, whatever you’re doing, you can do it better. It likely can be done faster, more efficiently and result in lower costs, higher profits and improved customer satisfaction.
That’s the basis of the many continuous improvement and quality programs that are ubiquitous to big businesses and increasingly finding their way into smaller businesses, including those in the aftermarket. The names are likely familiar – Six Sigma, Kaizen and lean manufacturing, to name a few – and they have been around for years. The companies that use them swear by them – they’re core to their management philosophy and day-to-day operations.
“The common theme is continuous improvement, which is what I prefer to call the whole effort,” says Dave Kwinn, a business coach with the Milwaukee School of Engineering. “I think it’s much more palatable than some of the other terms which can have some negative connotations. But how can anybody disagree with continuous improvement?”
Companies that have programs in place do not disagree, nor do they object to the many benefits continuous improvement brings.
Frank Camerota, owner of Camerota Truck Parts, says they implemented lean manufacturing techniques about eight years ago and then went through the ISO certification process about four years ago. The company, which has extensive remanufacturing operations, is currently ISO 9001:2008 certified.
“I would see four people doing the same job four different ways in my own company,” Camerota says of the catalyst for pursuing more formalized operational procedures.
“We started with lean manufacturing. It forces you to break down each step of your manufacturing processes,” he says. “Then you measure wasted time and examine every step and it just takes the waste out of everything.”
The result was greater productivity through fewer steps. The next stage, he says was to become ISO certified, a process which required systemized, formalized documentation of every facet of the company’s operations. While the lean manufacturing efforts focused on time and waste, ISO was more concerned with repeatable quality according to written procedures.
“It focuses on ever-improving quality and not as much on profitability or efficiencies,” Camerota says. “In other words you could easily have a super ISO program and go right out of business.”
Combining ISO certification and lean manufacturing have proven effective. “You need both of them because they do complement one another. In today’s business world, you need both. You have to be efficient to get your price down and you have to maintain quality.”
GETTING STARTED
While there are numerous continuous improvement programs – often tailored to fit specific requirements such as small business needs, or manufacturing or front-office functions – testing the waters and finding a good fit for your company does not require a large investment or extensive training.
Bill Wade, of Wade and Partners, points out there are numerous online resources and books to get you started. Talking to peers or suppliers who have implemented programs is another strategy. For the more complex programs, such as Six Sigma, it may require a little more effort.
Kwinn suggests selecting an employee who wants to learn more about continuous improvement, has a comfort level with math and graphs, and thinks operationally. Then send that employee to training or classes. Many community colleges offer this as part of their continuing education curriculum.
One program, 5S, will hold more appeal for the typical aftermarket distributor and service provider. “5S has to do with the orderly workplace,” says Wade. “Six Sigma is more of a philosophy of trying to work quality up to a certain level.” Because of its more academic approach, he says, smaller aftermarket businesses usually won’t be able to use Six Sigma to its full potential.
Six Sigma uses a set of statistical analysis tools to eliminate defects, ultimately allowing for a maximum of just 3.4 defects for every million opportunities – a success rate of 99.9997 percent.
5S on the other hand is more readily implementable and easier to deploy throughout a company. It, like Six Sigma, is based on a Japanese business philosophy.
“I always would start with 5S,” says Wade. “It’s universal. There is no place that it does not have a place. It’s common sense. It works and it works well.”
When translated to English, the five steps to 5S are:
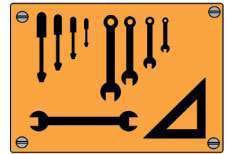
Sorting – Take a work station, such as service bay, and determine what the essential tools and items are for the functions performed there. Discard or store anything that is deemed unnecessary.
Systemizing or Simplifying– This requires putting those essential tools and items into orderly, ergonomic locations that maximize workflow. For instance, this step could result in tool shadow boards that keep tools in exact locations and complement the task at hand.
Sweeping or Shining – Clean the area as thoroughly as possible and keep it that way on a daily basis. Initially, this may require a fresh coat of paint and a lot of elbow grease.
Standardizing – This supports the previous three steps by committing them to routine. Everyone should embrace what’s been accomplished to this point and know their responsibilities for maintaining it.
Sustaining – Conduct regular reviews to ensure that the previous steps are being followed and that the focus to do so is still strong. This can include thinking of new ways to improve on the previous steps.
“5S should be the first step and it gets everything cleaned up and safe,” says Kwinn. “That is fundamental. You have to do that first. You usually will pick up a lot of benefits from that right off the bat.”
After all, you can’t reliably see issues and problems if there is too much clutter and confusion preventing a clear, analytic view.
Kaizen, another Japanese philosophy, is focused on continuous improvement in all areas of a business. While the implementation is a change in culture companywide, Kaizen tends to be more event driven.
According to Wade, it’s a methodology where you’re taking a specific problem and solving it through a Kaizen event. “If you didn’t call it a Kaizen event, it would be ‘we’re all going to go out in the shop, look at this problem and get it settled.’ I guess it has a little more panache if you call it a Kaizen event.”
Going lean is another strategy that involves process mapping to discover redundancies, opportunities for errors and other inefficiencies. While often called lean manufacturing, it is applicable to all areas of a business, from accounting to warehousing.
Once you analyze any given procedure, you likely will be surprised at the inefficiencies you discover. Some may seem minor at first, but when compounded over several times a day, it can add up quickly.
Start by establishing a baseline. For instance: how many times was a part touched before it was installed on a unit and out the door? How many motions are wasted? Does the technician have all of the tools he needs and are the tools readily and conveniently accessible? Does the technician have to leave the bay to go searching for needed tools or items?
Kwinn says a typical approach is to analyze a procedure from start to finish, using post-it notes to mark each step. This helps you better visualize the entire process in aggregate, identifying areas for improvement.
“A lot of it is common sense,” says Camerota. “But unless you put it together, you can’t see it.”
According to Wade, the common sense appeal is what makes these programs so successful. He says it’s creating “a common language” to create “a common approach to a problem.”
THE BENEFITS
Often the benefits of implementing a continuous improvement program are immediate and significant.
“Lean is dedicated to elimination of waste,” says Kwinn. “So you go through whatever operation, and you’re looking for waste. Typically the numbers are something like half the time someone is working is wasted time in the sense that it’s not something that a company wants to pay for.”
The change in culture also can positively affect employee attitudes.
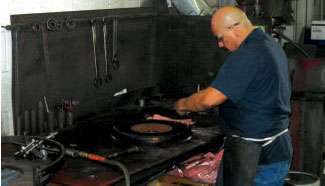
“As long as you don’t treat it as the program du jour, you need to really press it,” says Wade. “This is something that makes sense to everybody on a gut level so if you can keep the implementation somewhat simple but stick with it, I think it works as much for morale as it does anything else.”
The morale benefit can extend throughout the company and often justifies the program in and of itself. Employees take more pride in their workplace when it is clean and organized, and by eliminating redundancies and errors, more pride is taken in their work.
“Nobody gets up in the morning and says ‘how can I screw up at work today?’” says Wade. “They want to do the best job they can. I think it’s up to management to provide them things like Six Sigma or the quality tools in order to get that done.”
The benefits extend externally as well.
“We’ve improved customer relations. We’ve cut down dramatically on both warrantable failures and non-warrantable failures,” says Camerota. “Because we have corrective actions and we focus on things even if they aren’t Camerota problems. We don’t care who the problem belongs to, just how can we avoid it in the future?”
But to yield the ongoing benefits, the programs have to be maintained. These are not one-time events, and the binders of written procedures are meant to be revisited on a regular basis, not shelved and forgotten.
Camerota says in addition to having an internal team that conducts audits, ISO requires annual audits by an independent team, and it’s not inexpensive.
MISTAKES TO AVOID
Whichever program your company pursues, there are common mistakes to avoid as well as universal practices for success.
* For starters, it has to be a top-down commitment. The owner and top managers must not only embrace your continuous improvement program, they must lead by example. It does not send a good message when employees are working hard to maintain a clean, orderly work environment and the owner’s office looks like a war zone.
* Once the program is implemented, it must be seen through to completion. Starting and stopping and starting again will doom your efforts.
* It must be communicated clearly to every employee. They must understand the goals and the benefits. And, since processes and people’s work will be coming under close scrutiny, it will put employees at ease to know they aren’t being evaluated, the process and workflow is what is being analyzed.
“You have to change the company culture, and it isn’t easy sometimes,” says Camerota. “People do not like change. You get resistance for everything. You can change the toppings on the pizza at lunchtime and you get resistance. But once employees begin to understand that this is the way it’s going to be and this is the future and management is on top of this, they have to follow it, they have no choice. It’s not negotiable.”
* Start small and deploy the program in one specific area. Do not try to revolutionize your entire business all at once.
If you are considering whether continuous improvement will work for your business, Kwinn offers the following advice.
“If your metrics have not improved consistently over the past several years, then I think you really should start questioning what you’re doing,” he says. “For example, if your profit ratios, your inventory turns, your shipping performance or your sales growth have stayed more or less the same for a number of years, you’re really not making much progress.
“Continuous improvement is about progress and picking the things that are really going to make a difference in your business and then figuring out what you have to do to make them better.” n