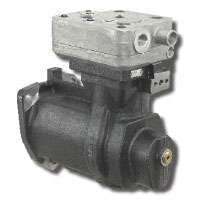
Eight ways to protect a tractor-trailer’s air supply
1. Remember Size Matters
The selection of every component in an air system should take into consideration exactly what will be powered, and how much air will be needed.
Like every other part on a truck, compressors and air dryers are sized for specific tasks. For example, a 13.5 CFM compressor may give a tandem trailer all the air it requires, but it will likely fall short if the tractor begins to haul a multi-axle Michigan combination, even if the drivetrain was strong enough to pull the load.
In fact, the compressor is only expected to build air up to 25 percent of the time. Duty cycles can be stretched to the limit by adding more air-powered accessories, making an unusual number of stops or leaving excessive leaks unaddressed.
If the compressor is overworked, a number of challenges can begin to emerge. The diameter and length of a discharge line, for example, might not be able to compensate for the warmer air coming from an overworked compressor. If that happens, oil will begin to pass through the system.
Meanwhile, the air dryer needs to be sized to handle the volume of air being pumped out by the compressor itself.
Aside from falling short in the battle against moisture and drops of oil, an overworked dryer will reach higher temperatures, and that can break down the related desiccant. These tiny particles have been known to work through air systems and clog the tiny orifices in ABS valves, jamming brakes into an on or off position.
2. Seal Everything Tight
Any air that passes between the tractor and trailer will need to travel through the gladhands, so a secure seal plays an important role in delivering that air.
There should be little surprise that the gladhands’ seals wear out over time. In addition to the constant twisting that comes during coupling and uncoupling, any rubber will deteriorate over time.
Once these seals begin to degrade, drivers will begin to report hearing leaks when they disengage the parking brake or apply the service brakes. If the leaks continue, more air will be consumed, leading to an overworked compressor and air dryer.
The good news is drivers can replace worn seals with ease, as long as they are given a supply of spares. The seals even can be upgraded to polyurethane versions that tend to last longer than their rubber counterparts.
Of course, the gladhands are not the only potential source of leaks in these systems that involve an array of fittings, seals and connections.
There is a simple check to determine if there is a leak. After building up the air until the governor cuts out, allow the pressure to stabilize for a minute and then watch the air gauge for another couple of minutes. Then apply the service brakes and hold them in place for two minutes. If the gauge registers a drop of more than 4 psi plus 2 psi for each trailer, there is a leak that needs to be addressed.
3. Keep It Dry
Any truck that operates in northern climes will rely on an air dryer to prevent moisture that can transform into ice. However, moisture can present problems in warmer environments as well, turning contaminants of all sorts into a muddy sludge that can slow the movement of valves.
It’s why these dryers deserve some ongoing attention of their own.
If water is freezing at the base of the air dryer itself, for example, the unit’s heater may not be receiving enough power. This situation often can be addressed by replacing a fuse or fixing anything that interferes with the heater’s circuit, such as a loose connection or a corroded wire splice.
But signs of moisture may not always indicate a problem. It can take several weeks for a retrofitted air dryer to catch up with the moisture in a system that has not been equipped with a dryer in the past. Some condensation also can be expected during trips where temperatures vary by more than 30Âş F.
4. Keep It Clean
The potential contamination in an air system is not limited to moisture, either.
As small as the opening in a gladhand appears to be, it offers plenty of room for debris that can form a barrier between the tractor’s air supply and the trailer. Shops have seen these spaces filled with everything from grass and grit to beehives and cigarette butts.
The air still may be able to pass through this debris during a gentle brake application, but if the brakes are applied suddenly, the debris can compress and plug the air line. The result is a lack of brake power.
A few minor upgrades can make the difference. Inline filters and gladhand filters, for example, can be added to form a protective shield that traps particles as small as .0003 in.
Added protection also is available for times when the tractor and trailer are uncoupled. Options that will plug a disconnected gladhand, much like a pacifier that plugs a baby’s mouth, will help to ensure that unwanted debris like those cigarette butts are kept out of the system.
5. Thaw With Care
Trailer technicians and drivers alike have been known to thaw frozen valves with liquid de-icers, but these fluids can lead to other problems. Options ranging from isopropyl alcohol to ethylene glycol antifreeze can cause the O-rings inside a brake valve to swell, and will break down the lubricants that protect internal pistons. Eventually, these issues can cause the valves to stick into place.
When de-icing fluids are used at all, only a small amount (such as 1/8 oz.) will be required, since it’s actually the resulting vapor that thaws the frozen components.
Of course, an alternative in the form of the warming touch of a torch’s flame can present a challenge of its own. The sudden and severe heat source can melt the rubber inside a valve.
It isn’t the only way that a torch can cause damage. A trailer technician who is welding brackets onto a trailer’s coupler plates may not stop to realize that, by heating the plates, he also is melting nearby air lines. When work like this is being completed, it is a good idea to place a piece of wood between the frame and the air line before applying the torch.
Consider what will be powered and how much air will be needed when selecting air system components.
6. Check The Chambers
Given how close they hang to the road, there should be little surprise that brake chambers can be battered by debris, but that damage also can be more than skin deep. Dents may be a sign of internal issues such as compromised seals, which can cause brakes to drag.
The choice of a replacement chambers can make a lasting difference to the system’s performance. As similar as the designs may appear, different brands can generate wide variations in stopping forces. This will make it important to install the same design at both ends of an axle.
Keep in mind that value-priced models may present some challenges of their own. Corrosive de-icing compounds have been known to travel through the vents in some designs, and some chambers simply are clamped together rather than welded shut, potentially exposing technicians to the explosive po wer of a compressed spring.
7. Be aware of the weakest links
Kinked lines, poorly installed fittings, faulty valves or damaged chambers all can be causes of sluggish performance.
Indeed, no matter what individual components might promise, the overall system will only be as strong as its weakest link. A 3/8-in. hose rated at 1,000 psi, for example, will only be as strong as the 500 psi coupling that is used for a connection.
Different manufacturers also accept different tolerances in the products they make, meaning the fits of any connections can vary from one brand to the next.
8. Don’t vary the valves
As similar as valves might seem — right down to the position of the ports for the air lines — there can be big differences in the internal components. Some models will relay air immediately, while others remain closed until a specific crack pressure is achieved. The valves installed in an individual system are designed to feed air to each wheel end at the same time.
A decision to force a different valve into place can throw that balance out the window, causing aggressive brake components to wear out more quickly, or actually affecting how the trailer will track when coming to a stop.
But if a shop is careful to install the right components, everyone will have a chance to breathe easy.
•Sources: Bendix, Haldex, Meritor WABCO, Phillips, Truck Watch Services