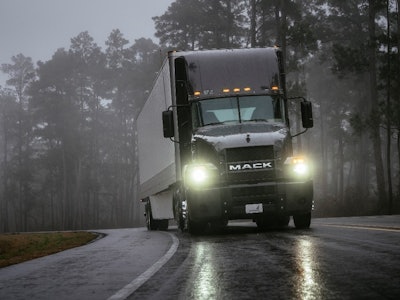
Hurricane Debby and its aftereffects are still spreading flooding rains across much of the eastern U.S., flooding homes, business and yes, trucks. Bendix Commercial Vehicle Systems offers these tips for inspecting and reconditioning flooded vehicles.
"One important thing to note is that electric vehicles (EVs) are becoming more common and service procedures for EVs require special training," says Randy Salvatora, engineering manager of vehicle systems. "Do not approach a previously submerged hybrid or electric vehicle until the high-voltage electrical system is inspected by a qualified technician."
Appropriate personal protective gear should be worn when washing or working in flooded vehicles.
Salt water versus fresh
First, determine if the water affecting the truck was salt or fresh. If it was salt water, begin replacing parts as soon as you can. Salt water is extremely corrosive and can remove lubrication and put some parts at risk for unexpected and premature malfunction. Any brake system valve that has been submerged in salt water must be replaced.
Air compressors, air reservoirs, antilock brake system relays, modulators, wiring harnesses and brake actuators must also be replaced.
"Salt water corrosion is also a threat to brake mechanisms, since it increases the likelihood of rust jacking of the friction material and accelerates corrosion of critical surfaces," Salvatora says. "So, we recommend complete replacement of the foundation brakes to prevent a potential future failure. And if it's not clear whether the water was fresh or salt, play it safe and follow the salt water guidelines."
When replacing any pneumatic system components subjected to flood water, disconnect all contaminated air tubes and hoses, flush them with clean water and blow them out with air to remove contaminants.
Fresh water guidelines
For a power unit or trailer submerged in fresh water, begin by carefully power washing the vehicle, including the foundation brakes. Rubber parts and sealing interfaces should not be directly sprayed with the high-pressure jet; they can be damaged irreparably, as can exhaust ports.
Most valves, while in an unapplied state, are open at the exhaust port. This means if any exhaust port is submerged, the water has infiltrated the system and can lead to future malfunction. Do not attempt to start a vehicle if fresh water has entered the air compressor or dryer through the air system intakes, Bendix says.
These are the steps to check the various parts of the air brake systems:
Vehicle valving
- Inspect each component in the pneumatic brake and accessory systems.
- Drain any pressure remaining in the service reservoirs.
- Mark and remove all pneumatic and electrical connectors at each valve.
- Check for evidence of water or contamination inside the connectors, air hoses or the component itself.
- Carefully inspect any wiring harness connections. Water infiltration at the connector can lead to corrosion of the wiring harness inside the insulation. This can lead to intermittent continuity, increased resistance and time-consuming electronic diagnostics.
- Carefully use dry compressed air pressure (from a stationary compressor or similar) to blow air through the pneumatic tubes and hoses. Watch for evidence of water or contamination.
- If water or contamination is found inside the component, replace the component.
- If no evidence of water or contamination is found inside the component, reassemble the component to the associated lines and fittings.
- Repeat this process as you continue to inspect all the valves in the air brake system. Replace any nonfunctioning valves or those showing evidence of ingestion of water or contaminants.
- Inspect tractor and trailer glad hands and the supply and control hoses. Water and contaminants frequently enter the air brake system through unprotected glad hands.
Charging system
- Inspect the air intake, compressor and air dryer for signs of water or contaminant ingestion.
- Carefully use dry compressed air pressure from a stationary compressor or similar to blow air through the pneumatic tubing and watch for evidence of water or contamination.
- An electrically driven air compressor that has been submerged is not serviceable and should be replaced.
- Use dry compressed air from a stationary air compressor or suitable portable unit to get any residual water out of the service tanks.
- Air dryers remove moisture in compressed air but they will not remove moisture that's present in the system beyond the service tanks.
- After reconnecting pneumatic lines, install a new or properly serviced air dryer to aid in removing any residual moisture from the air inlet.
If there are signs of moisture or other contamination, all pneumatic air brake components should be replaced. Once water or contaminants get into any of the air brake components, it's impossible to completely clear the system without total disassembly. Consider also the guidance in the TMC Recommended Practice 617A for contaminant elimination procedure for tractor, trailer or dolly air brake systems.
Wheel-ends and electronics
All wheel-ends should be checked for water, which increases the possibility of corrosion between drum brake lining material and the shoe table (rust jacking), and can also pool in drums when left standing, increasing the risk of corrosion.
Check the integrity of the friction couple between the friction and disc or drum. Water-filled loading docks may not immediately come to mind as flood events, but can have the same impact to wheel-end components such as slack adjusters.
Remove any fittings and mounting stud nuts and orient ports downward to verify that no water has entered brake chambers through the air lines. If water is present, replace the actuator. Follow the appropriate wheel-end relubrication procedures, including re-greasing slack adjusters.
Assess braking and safety electronics components to conduct a diagnostic download on systems such as ABS, ESC (electronic stability control) and collision mitigation controllers, including any front or side radar units. Electronics will validate through self-check in most cases. If the electronic control unit (ECU) is operable, it will check the necessary solenoids, sensor, harnesses, etc.
A visual inspection is still necessary. Residual mud must be cleaned off the radar and radar cover. If any cracks or damage are observed, both the radar and cover should be replaced. Make sure to inspect the seven-pin electrical connector interface between the tractor and trailer as well. Corrosion at this connection is a common cause of flickering lights and intermittent power to the trailer ABS system.
Bendix recommends two technical bulletins available in the Bendix Document Library at B2Bendix.com: Flood Damage: Bendix Recommended Procedure for Trailer and Dolly Control Systems That May Have Been Submerged (TCH-003-048) and Flood Damage: Bendix Recommended Procedure for Power Vehicles That May Have Been Submerged (TCH-003-049).
Getting back on the road and follow-up support
If the checks turn up no evidence of water or contamination, conduct a thorough test of the air brake system and ABS before returning the truck and trailer to service. Between the flood waters and power-washing, it's possible that ABS wheel speed sensors may have been moved from their normal position. Push them back into contact with the exciter ring by hand and, when the wheel turns, normal wheel-bearing play will adjust the sensor position.
"We recommend retesting and diagnostic checks of the electronic systems after the initial post-flood testing," Salvatora says. "Additionally, make sure you're following other vehicle and system manufacturers' guideline: Flooding can have bumper-to-bumper effects and you can't be too careful."