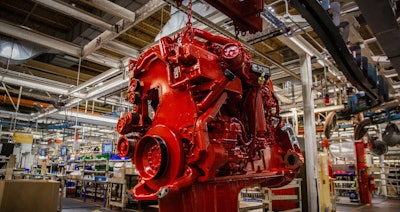
Circular economies, such as those provided by remanufactured parts, are increasingly important for the resiliency of supply chains and the environment, panelists said on an Engine Technology Forum webinar Monday.
Representatives from engine manufacturers, including Cummins, and companies such as Stanadyne and Johnson Matthey discussed the role remanufacturing plays in their business. Patricia Covington, executive director of ReCon General Management at Cummins, says her company has been remanufacturing parts since the early 1960s. Cummins quickly found it was good business and resulted in lower customer repair costs and downtime.
"That was really, really critical," she says.
The remanufacturing process starts with the dirty core product. Cummins and the other companies on the call said once the core component has reached the end of its useful life, they want it back.
[RELATED: Cummins partners with Platform Science, showcases new X15]
"That dirty core is the most important element for us," Covington says. The company tries to make it easy for the customers to return the core. Once they have it, it's disassembled, cleaned and is remanufactured for use again with the same expectations for its performance as a new product.
Like other panelists, Cummins uses its remanufactured products to buffer against disruptions in the supply of new materials and to provide a more cost-effective option for its customers. All of the companies represented stressed the importance of the remanufacturing life cycle.
"The way we've thought about it over a number of years is that we're giving customers an option to continue to use a product they've fallen in love with," Covington says.
It starts, Covington says, with a growth phase. A new product is introduced, and at least initially, there's a low core return rate and field cores are not available. Eventually, as more products hit he market and age, remanufacturing starts and slowly ramps up to a mature phase, where cores are being returned and field cores are available at reasonable prices. Remanufactured and new parts may be produced at the same time in the beginning of this phase, but the production lines are kept completely separate.
"Once you introduce a remanufactured component on a new engine, it is no longer a new engine," Covington says.
Kevin Schrag, manager of remanufacturing at John Deere, says all of that company's remanufacturing is done out of Springfield, Mo., John Deere is part of the Remanufacturing Industry Council (RIC), which defines remanufacturing as "a comprehensive and rigorous industrial process by which a previously sold, worn or non-functional product or component is returned to a 'like-new' or 'better than new' condition and warranted in performance level and quality." It is not, the council says, the same as recycling or repairing, though both of those processes are involved in remanufacturing.
[RELATED: MEMA council seeks industry input for history of remanufacturing initiative]
Jeff Sutherland, drivetrain product manager and chief engineer at Caterpillar, is also part of the RIC. He says his and other companies are designing for remanufacturing, making products easier to remanufacture with purposeful initial designs.
"Oftentimes, our ability to remanufacture something is limited by decisions that are not forward-thinking," Sutherland says.
He says the RIC, in partnership Trane Technologies, the Rochester Institute of Technology and Caterpillar, has developed a plug-in for computer assisted design (CAD)software that interrogates designs to identify failure modes and remanufacturing difficulties.
"The best way to remanufacture something is not to have to remanufacture," Sutherland says.
Srinu Gunturu, chief engineer at Stanadyne, says his company is one of the leading remanufacturers of diesel common rail injectors, sending more than 400,000 of the components per year back into the market. Stanadyne, he says, embraces a holistic approach to manufacturing to reduce waste and improve efficiency, both for the company and for its customers.
"As we are innovating for the future, ensuring the technologies are environmentally responsible are more important than ever," he says. Stanadyne reuses 80% of a components original material, Gunturu says, resulting in a product that is made to exact OEM specifications.
Marge Ryan at Johnson Matthey says her company, which focuses on aftertreatment, looks at designing a durable, resilient aftertreatment solution that can achieve high mileage with no or minimal parts replacement. Part of that is recovering the platinum group minerals (PGMs) that are used in the process, designing its solutions for regeneration and other processes that make them more sustainable. This creates a circular economy of PGMs — which are not geologically abundant, but are important in a variety of industrial applications.
"Because PGMs are not downcycled, secondary material is identical to primary material," Ryan says, and ICE vehicles are not only the largest user of PGMs, but also one of the largest mines for PGMs. This is important, Ryan says, for the resiliency of the supply chain. About 60% of the PGMs used in newly fabricated products and aftertreatment catalysts are now made from recycled metals.
"We work with customers to close the loop whenever possible," she says.