Oil Has A Story To Tell
Few people would take their health for granted to the point of avoiding checkups and never submitting to a blood test. There are simply too many potential risks that could go unnoticed until it’s too late.
Analysis of blood samples can help spot warning signs – high cholesterol or diabetes, for instance – before serious health problems become untreatable.
If there is an equivalent diagnostic tool for a truck, it comes in the form of an oil analysis. Each sample of the lubricant can be used to identify the trends that guide preventive and predictive maintenance measures.
It is the type of information that may be the last line of defense before a catastrophic failure.
Dan Arcy, OEM technical manager with Shell Global Solutions, says he heard a clear example of that line of defense when he attended a meeting of the Technology & Maintenance Council. There, a fleet representative spoke about how it used the results from an analysis to determine the need to replace an idler pulley after 25,000 miles. Without the report, the truck would have blindly continued its trip before throwing a belt and becoming stranded on the side of the highway. “You can identify a lot of these things early,” he says.
Consider the information that can emerge. A contaminant such as silicone could draw attention to loose air intake components that are allowing the engine to ingest dirt, notes Shawn Ewing, ConocoPhillips’ technical coordinator for heavy-duty lubricants. And a spike in aluminum could be traced to a breakdown in the flux used to weld together the tubes of a charge-air cooler.
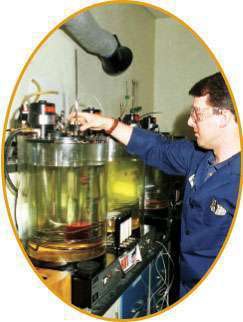
There can be a clear connection between wear metals and specific components. Levels of chromium, for example, can indicate that piston rings have been damaged, while readings of iron or aluminum can be worrisome depending on the metals that were used to create the engine block or cylinder liners. Maintenance teams that identify a spike in a level of copper may be able to write it off as the switch from one oil formulation to the next – it can sometimes be traced to the thin varnish on copper tubes that run through some oil coolers – but it also can be from issues with an exhaust gas recirculation (EGR) system.
Some of the engines introduced in the past five years are more prone to coolant leaks, adds Mark Betner, Citgo’s product manager, heavy-duty lubricants. A “good little percent” show a significant amount of coolant contamination.
At the very least, each analysis will help determine if existing drain intervals are frequent enough to maintain the protective qualities of the oil that faces the constant assault of everything from high temperatures to loads of soot.
ADDING VALUE
In addition to helping maximize truck life and performance, offering your customers an oil analysis program can provide them with other benefits as well.
Betner notes how the benefits go beyond predictive maintenance strategies, referring to one fleet in Salt Lake City which attaches the data to every used truck that it sells, offering proof that oil changes were properly scheduled.
“If you had a good maintenance record and you attach a complete oil analysis history from the birth of the vehicle, you will have a much better chance of increasing the value of that vehicle,” Betner says. The strategy seems to have worked. The fleet now recovers an extra $3,000 to $4,000 in the value of each Class 8 truck it sells.
“It does assist you with your discussions with the engine manufacturer, with the OEM,” adds David Pack, international, commercial and industrial marketing manager for Valvoline. “They could be part of a tool to use for warranty protection and even the selling of that truck … you have some history of how that engine has performed.”
Still, the accuracy of each analysis will largely be dictated by procedures in the shop. “You’re looking for a trend,” Arcy explains. That means samples need to be taken the same way from one report to the next.
While there are many ways to take oil samples, a shop should adopt a consistent approach to maintain the integrity of the results, he says. Techniques range from undoing the drain plug in the sump and taking a sample after allowing the lubricant to drain for a few seconds, to using tools such as the valves that reach into oil galleries like the needle used to air up a basketball. The most important thing is to do it the same way from one sample to the next.
Shops even need to consider how long a truck has been running before extracting a sample. If the engine sits still for too long, any soot or fuel in the mixture will settle. In contrast, a warm engine will ensure that the entire oil sample is properly mixed.
The related paperwork requires some attention of its own. If a fleet has set oil drain intervals at 25,000 miles, shops have been known to record that figure as the mileage at every oil change. When it comes to an analysis program, it is better to include an exact mileage.
The information about a specific engine model will be particularly vital. The sump on a Detroit Diesel engine, for example, will likely be larger than the one on a Caterpillar design, Pack notes. The available volume of oil will affect how quickly the lubricant depletes.
“Those kinds of things are critical,” Arcy says, noting how information about a volume of any added oil can be helpful as well. “The better information you get in, the better information you’re going to get out.”
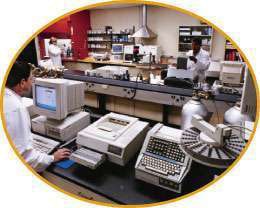
The sample also should be delivered to a lab as quickly as possible. Shell’s labs, for example, will analyze a sample within 48 hours, which can deliver timely information about a truck that needs to be pulled off the road. That opportunity will be lost if a shop lets the samples sit on a work bench until the teams work through all 10 sample jars in a box.
“There’s options where they are postage paid already, and that makes it easier,” Arcy adds.
There is another reason not to collect multiple bottles before sending them away for an analysis, Pack says. If anything is not labeled at the time a sample is collected, there is the potential of confusing the results.
The choice of a lab can also affect the amount of time that a shop needs to wait for results, he notes. “Choose the lab that is appropriate to where you live. If I live in Lexington, Kentucky, I don’t need to send it to Denver to get it analyzed.”
The related reports have made it easier for shops to identify the issues that an oil analysis can spot. Shell’s Lube Analyst program, for example, identifies power units that require immediate attention because of a problem such as a coolant leak. Those generate a call that is linked to the specific unit number. Meanwhile, the standard reports include a color-coded report card. A green report means that everything is OK, while a yellow color identifies equipment with an issue that deserves attention. An iron content of 75 ppm may be acceptable to an OEM, for example, but it could still be flagged if previous samples tended to contain levels of 50 ppm. “It’s about pointing out those real step changes,” says Arcy.
“Once you learn the tools of your program, you can take a lot of data and boil it down to one spreadsheet or one managerial report,” Ewing adds, noting that graphs can be particularly useful when helping to identify trends at a glance. “A picture is worth a thousand words.”
SERVICE SWEET SPOTS
Then there is the potential to help customers reduce costs by extending their oil drain intervals.
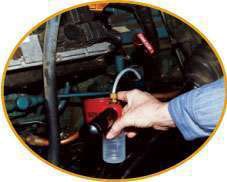
The interest in extending drain intervals did begin to wane in the early days of EGR systems, when oils struggled under a massive increase in soot loads, but today’s equipment and formulas are up to the challenge, Ewing says. That can be particularly welcome news for your customers who are seeking new cost-saving strategies in the middle of a tough economy.
Oil may be relatively inexpensive, but when it is coupled with the cost of a filter and labor, that can add up to as much as $150, Betner says. If 30 vehicles required six changes per year at a cost of $18,000, a 30 percent cut in the number of changes could save $6,000. That still may not sound like a significant share of a maintenance budget, but the savings really add up once fleets consider that each of the trucks are spending more time on the highway and making money rather than sitting in a shop.
It is a message that shops should embrace, he insists. “That helps the customer, and if you’re helping the customer you’re helping yourself.” The service teams will also be able to identify components they should replace, rather than leaving the work to a shop that happens to be located near the source of a breakdown.
“You, in a sense, become the data manager and the communicator of what is going on with their oil,” Betner says. “If [shops] get a critical alert, they can forward that alert to the customer by email … they could become the conduit of information to prevent those catastrophic failures.”
Besides, oil will wear out, and the analysis will ensure that the lubricant is offering the all important chemical defense that it is designed to provide. “There is testing information that comes back and tells you if the oil is giving up its last breath, chemically speaking,” he adds, referring to measurements such as Total Acid Number or Total Base Number. If a fleet is using 15W40 oil in cold temperatures, an oil analysis also could identify the soot loading which could cause cold weather start-up problems.
It is the type of information that makes a shop that much more important to a fleet’s business plan.
There is an environmental benefit to the process, too. “There is no sense throwing away good product just because you don’t know the facts,” Betner says, noting how programs such as EPA’s SmartWay initiative track issues such as the amount of oil that is disposed. “Everybody is concerned with stewardship these days.
“If you’re going to go forward with a program at a service center, you should train your technicians,” he adds, referring to the importance of the information. Some simple literature or videos from the providers of an analysis program can help to explain the steps that are being taken. “If I was a service center, I would even invite some of my customers to a little workshop, maybe for an hour.”
“The shop gains customer confidence and, if you will, his loyalty,” Ewing says of the entire process. “If it seems the shop is in a caring mode about the ultimate life of the customer’s engine and components, he’s going to come back and say, ‘This guy really cares … let him service everything I have.’”
The oil, after all, has a hidden story to tell. Shop personnel are the people who can ensure the story is heard.
“If you go through life without ever getting any blood work,” Betner continues, “you’re flying blind.” n