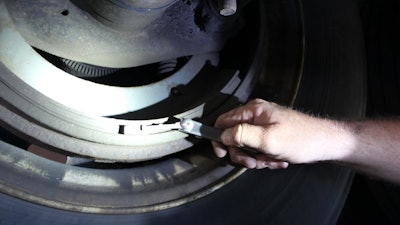
[This article was originally published in 2007 by Trucks, Parts, Service. It has been updated to include more timely information.]
When rebuilding an engine, no conscientious technician would toss in a new set of rings and neglect to look at the condition of the liners, pistons, valves, heads and other vital parts.
Why? Because the engine is a system of components working together, and individual components depend on each other to perform properly.
The same is true of the foundation brakes. Inspecting the condition of all brake components when performing a brake reline will explain premature lining wear or brake performance problems and head off future troubles.
Most experts agree that minimum acceptable lining thickness is 1/4 inch, which should be slightly above the rivet heads. There is a possibility of drum scoring or camshaft turnover and reduced braking performance when the lining is less than the minimum thickness.
Regard reline time as an opportunity to restore total system performance.
Start with the foundation brakes
A good beginning is to take an up-close look at an application of the brakes.
Watch for excessive deflection and loose or broken parts. Check cam splines for wear, as excessive wear allows lost motion between the slack adjuster and camshaft. Replace the camshaft and the slack adjuster if there is more than .020 inch of free movement between them.
When applying the brakes, check the slack adjuster for proper brake adjustment. The ASA manufacturer will have detailed instructions on how to perform this inspection, Meritor says.
Also check the clearance between the slack clevis pin and its bushing. Clearance should not exceed .020 inch. When reinstalling a slack, use an anti-seize compound on the camshaft splines to make it easier to remove next time.
Interpret shoe wear
Don’t just throw old shoes in the core bin; look at them. Lining wear should be even around the circumference of the brake assembly, and from inboard to outboard. More wear on the bottom, top or one side could indicate that peripheral brake hardware is worn. When that’s the case, brakes can’t be adjusted properly.
For example, look for tapered wear, a condition where the shoes show more wear at the inboard or outboard side, rather than wear that’s uniform. Worn anchor pins, holes and bushings or outer S-cam bushings can allow applied force to push the shoes to one side, resulting in tapered lining wear.
This condition often is accompanied by outer edge abrasion on the brake shoes. This is caused by the shoes tracking out of alignment because of worn parts. Do not reuse shoe rollers and anchor pins.
[RELATED: Bendix Tech Tips touches on winterizing wheel-end, air systems, electronics and controls]
When removing anchor pins, don’t heat the spider and try to hammer them out. Heating removes the metal’s temper, and hammering a hot spider will cause permanent distortion, reduced brake performance and abnormal wear. If anchor pins are stubborn, douse them with a light, penetrating oil, let the oil work in and tap them out as gently as possible, or use a puller designed for that purpose.
Clean the spider with a solvent and wire brush and inspect for broken welds or cracks in the camshaft and anchor pin areas. Check tightness of the spider securing bolts and be sure the spider is not bent — the anchor pin holes must be parallel to the centerline of the axle. Otherwise, the shoes won’t track properly in the drum, and tapered wear will result.
Don’t confuse tapered lining wear with a high ridge on the inside edge of the linings. This is beneficial as it prevents a lip from being etched into the drum and makes drum removal easier. It also helps keep water and contaminants out of the brake assembly.
Unequal lining wear between the leading and trailing ends of a shoe might be the result of a weak return spring, a worn outer S-cam bushing or an out-of-arc shoe.
Attempting to adjust a brake with any of these conditions will result in dragging and high contact pressure at one spot of the lining, which could lead to rapid lining wear and heat damage to the brake drum.
Are any linings cracked? If so, it’s a good bet that they were loose on the shoe. This can be caused by a shoe that’s out of arc, rust buildup on the shoe surface or improper riveting.
When replacing the shoes, make sure the lining is tight and follows the contour of the shoe. Always check a replacement shoe’s dimensions — don’t assume it’s okay just because it has new lining on it.
When choosing new or rebuilt shoes or new friction material, stay with name brands as bargain products are likely to give you more trouble than you’d like.
If linings are contaminated with oil or grease, correct the cause before relining. The problem is almost always a leaking oil seal, too much grease on a grease-type wheel bearing or camshaft bushing or careless handling.
[RELATED: How to: Check for wheel-end seal leaks]
If the lining is otherwise okay, but an area no larger than 10 percent of the total lining area is contaminated by grease or oil, the spot can be cleaned with brake cleaning solvent, not gasoline or another substitute. If done improperly, this can lead to a brake imbalance condition.
Don’t overlook hardware, drums
Check cam bearing surfaces for wear and replace the cam if wear exceeds .010 in. A cam that’s within tolerance but has deep grooves caused by the seals can be reused, but it will admit abrasive contaminants and accelerate bearing and cam wear. The cam bearing should be replaced at each reline.
Carefully look at the S-cam and rollers for flat spots and irregularities. An irregular surface on these parts will cause brake noise and make brakes grabby and slow to release.
If in doubt, replace the camshafts on both left and right wheel ends. It is important to balance the brake systems, Meritor says.
Return springs are inexpensive and there’s almost no excuse for reusing them, but if you must, be sure they’re not stretched, broken or corroded.
Drums also can get leopard spotting, or black and/or gray martensite spots on the cast iron braking surface. If there are a lot of these spots, the drum should be changed as the martensite spots are harder and occupy greater volume than the cast iron. The martensite will result in fast wear of the brake lining, and eventual cracking of the drum from the stress. The typical root cause of the martensite spotting is lightweight drums being used in applications they are not suited for, says Marathon Brake Systems.
When reassembling, don’t forget to lube the cam bearing and seals, anchor pin bores and bushings.
Next to the brake shoes and linings, the brake drum is the most important component in the overall foundation brake system. One of the drum’s jobs is to absorb heat and dissipate it to the surrounding air. The heavier the drum, the more heat it can absorb. Turning and even normal wear removes valuable metal reducing the drum’s effectiveness and increases its inside diameter. This diameter change reduces the contact area of the new shoes, causing the lining to work harder which can result in premature wear and brake fade, Haldex says.
Even a new drum may not be round, and even if it is, mounting it incorrectly on the hub pilots can cause it to rotate unevenly (non-concentric). Haldex says to check for roundness, use a dial indicator to measure a mounted drum in the center of the rubbing path. Rotate the drum a full 360 degrees and refer to the drum manufacturer’s recommendations for maximum run-out.
An out-of-round brake drum can cause erratic braking, momentary low-speed wheel lockup and the automatic brake adjuster not being able to maintain proper shoe-to-drum clearance, Haldex says.
No matter how good a reline you’ve done, the linings must have a smooth, round drum to rub against. Haldex says if you want top performance, consider replacing the drum at every reline.
The key to a good reline is to remember that brakes are a system of components working together to get the job done. If part of the system isn’t right, the system isn’t right.
If you extend that line of thinking, the same is true of the entire vehicle. Wheel seals, bearings, axles — anything you touch during a brake job should be treated with the same respect given to the brake components.
Bring everything as close as possible to its original condition and you won’t be sorry. It costs more up front, but a thorough job will pay for itself in long life and trouble-free operation.
Bendix Commercial Vehicle Systems says while the basics of foundation drum braking technology haven’t changed much over the years, the increased braking demands under reduced stopping distance (RSD) requirements have made it even more critical to properly maintain drum brake systems.
Today’s brakes are capable of more torque than in the past, so it’s even more critical that they operate as designed. It’s similar to adding more horsepower and RPM to an engine; with higher performance, it’s more important than ever to properly inspect, maintain and replace parts, Bendix says.
Bendix Commercial Vehicle Systems