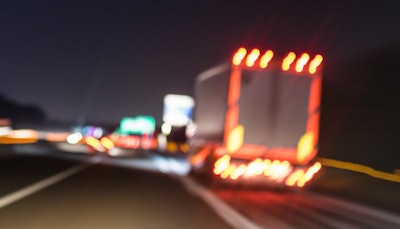
[This article was originally published in 2020 by Trucks, Parts, Service. It has been updated to include more timely information.]
No one wants to see a truck sidelined. Whether it be due to a breakdown, component failure or out of service violation, downtime hurts all customers' business. One of the easiest downtime incidents to avoid are lighting failures.
By providing comprehensive inspections, service providers can keep customer equipment on the road so they can avoid out of service violations or emergency repairs. And as light-emitting diode (LED) lamps have become more popular, inspecting lighting systems have never been easier.
Yet, despite that, infractions because of improper “lighting devices,” remain a sizable percentage of violations rendered during annual inspection blitz events. During the CVSA’s International Roadcheck in 2019, for example, there were 16,347 out-of-service vehicle conditions in the United States and Canada. Lighting devices ranked fifth with 1,875 violations (11.5 percent).
“Most LED lights that make up a turn signal, brake light, etc., go out in clusters. There might be a multitude of LEDs that are still operating within that specific light but there’s maybe three or four LEDs that are inoperable; that doesn’t necessarily mean the light is in violation,” says Kerri Wirachowsky, CVSA roadside inspection program director. “If the light can still be seen from the required distance for that light with the LED lights that are remaining, the light is not yet in violation.”
Peterson Manufacturing suggests performing a complete inspection of the lighting and harness connections.
Wirachowsky, who served as a roadside inspector for more than 25 years, says if technicians and drivers notice the few inoperable diodes, they can do pre-emptive maintenance and replace them before a violation ever exists.
“If you don’t repair what’s not working when it is noticed, eventually the next cluster is going to go out and [officials are] going to then cite a violation,” she says. “My point is it gives you a timeframe to fix the problem before it’s a violation. Don’t wait until everything goes out and it is a violation and/or out of service. That’s too late and just a bad maintenance practice.”
What service providers can do
Several lighting manufacturers offer tips for aftermarket service providers to ensure their customers’ truck and trailer lights are in good condition.
Mark Assenmacher, director of marketing, Peterson Manufacturing, suggests performing a complete inspection of the lighting and harness connections.
Major causes of light failures can include damage, corrosion, loose connections, poor grounding and excessive shock and vibration in the case of incandescent lamps, Assenmacher says. Some of these causes can be minimized by using LED lighting, which is much less susceptible to shock and vibration.
“Using good weather-resistant connectors such as AMP-compatible or other hard-shell connectors can help keep out corrosion at the connection point. Industry-standard type plugs, such as PL3 or P10, should be inspected regularly and dielectric grease should be used to protect the connection point,” he says.
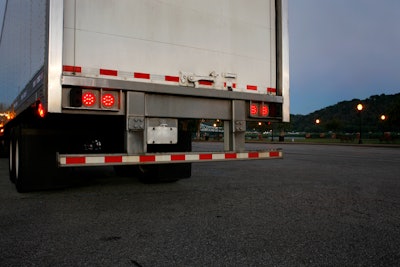
Assenmacher cautions, “If at all possible, test probes should not be used, especially on a trailer with a complete sealed harness and lighting system, as this may void any OEM warranty. Some lighting and harness manufacturers offer guides or maintenance posters to assist repair facilities with trouble-shooting.”
Mark Blackford, director, national fleet sales, Grote Industries, says when technicians are inspecting LED lights, they should be looking for cracked lenses, which can be caused, for example, by a forklift, a branch or a dock pad.
“Cracks will draw moisture into the housing. If you have a cracked lens, it’s amazing how much water will penetrate that lens and get into the light itself,” Blackford says.
He suggests visually inspecting the harness pigtails as well as the power cord between the tractor and the trailer. “If you’re not getting proper voltage to the trailer, you’re never going to have proper functioning LEDs.”
Blackford offers another pointer: if there are four taillights and one is burning dimmer than the rest, there’s probably an issue with the ground. Corroded terminals at the ground will sap the needed amps for a LED to light properly, he says.
Popular modular power delivery systems have snap-together connectors enabling OEMs to design electrical system configurations that supply electricity on a vehicle. However, if these systems are not maintained properly, they become susceptible to the elements and ultimately to failure, says Kyle O’Dell, director of engineering, Optronics International.
“Electrical connection points are the weakest link in the chain and each presents an opportunity for moisture to invade the system and cause corrosion,” O’Dell says. “Some fleets are proactive and work with their … maintenance folks to apply heat-shrink moisture barriers to all electrical connections as soon as they take delivery of new vehicles.”
Technician installs an LED light from Optronics International.
O’Dell says technicians inspecting LED lights should ensure all lighting is correctly installed and operating properly. Cables and wiring might have been bent during installation or through subsequent stress — both can cause cracks in its protective insulating layers.
Technicians should examine seals, connection points and cable and assess wiring integrity, because “a vehicle’s movement can adversely impact lighting and harness systems,” he says.
O’Dell says to inspect connectors regularly and apply dielectric grease as needed.
He adds, “Lighting and harness PM is like regular exercise. First you have to make it a routine and, once you start doing it regularly, the benefits are significant, noticeable and wide-ranging.”