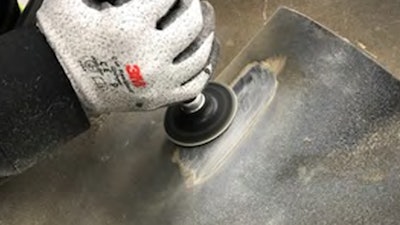
[This article was originally published in 2018 by Trucks, Parts, Service. It has been updated to include more timely information.]
One of the materials commonly used in heavy-duty trucks is Metton liquid molding resin (LMR), a tough and durable engineered plastic material used to produce large or thick molded parts.
Despite its popularity among manufacturers, 3M says not a lot is known about identifying and repairing Metton, which, as a substrate, requires a different approach than fiberglass (FRP) and sheet molded compound (SMC).
3M Automotive Aftermarket Division says it now offers standard operating procedures (SOPs) for repairing this material.
What is Metton and where is it used?
3M says light-weighting is a process that is a high priority for heavy-duty truck manufacturers. Efforts to reduce vehicle weight are driven by Corporate Average Fuel Economy (CAFÉ) standards and competition among vehicle manufacturers. Innovative technologies and materials have contributed to the ultimate goal of delivering increased fuel efficiency to the heavy-duty truck customer.
[RELATED: Phillips tips to control, mitigate electrical corrosion]
One area receiving significant attention has been the weight of exterior body panels. 3M says body panels have gotten lighter due to design, material and manufacturing improvements over time. One material that has increased in use for exterior truck body panels is Metton LMR.
Metton is produced using a closed mold process that helps deliver more consistent parts with tighter tolerances, improves manufacturing cycle times and enables increased design freedom compared with other materials and processes, 3M says.
This material is lighter than traditional fiberglass and SMC. Additionally, it is more rigid and impact resistant — especially in colder climates — than many plastics such as thermal plastic olefin (TPO). 3M says many exterior truck body panels today are being produced using Metton including hoods, roof and chassis fairings, bumpers and fenders.
Identification of Metton
Metton is black in color and is more rigid when compared to other plastics like TPO. When grinding or sanding during the repair process, 3M says Metton does not produce a cloud of airborne, itchy dust like FRP and SMC panels as it does not contain fiberglass fibers. Metton will grind and sand more evenly compared with other plastic materials.
[RELATED: Maintaining proper tire pressure presents 'huge opportunity in today's volatile fuel market']
For example, 3M says Metton doesn’t smear and flow as much as TPO can during grinding and sanding operations. Another indication of working on Metton is the unique odor produced when grinding or sanding the material.
Repairing Metton
Now that Metton has been identified, how is this material repaired? 3M has developed a SOP for a backside reinforcement repair and a cosmetic repair for composite materials that include FRP, SMC and Metton. 3M says repair procedures for Metton are surprisingly similar to the repair processes body technicians use for SMC and other plastics.
The most critical difference between repairing Metton and SMC is the use of an adhesion promoter such as 3M Polyolefin Adhesion Promoter. 3M says adhesion promoter is necessary to increase the bond strength between the repair adhesive and the surface of the Metton. This should be a standard practice when using adhesives on other plastics such as TPO and polypropylene as well, the company says.
A full library of 3M heavy-duty truck standard operating procedures is available.