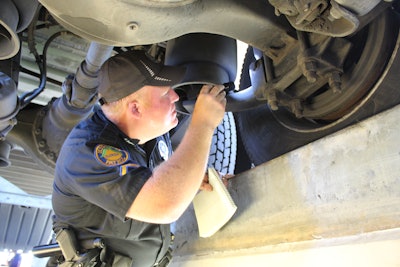
Brake drums help tell the critical story of overall brake performance, which is important since an overwhelming portion of violations — 45 percent during last year’s Commercial Vehicle Safety Alliance (CVSA) Inspection Blitz — were owed to bad brakes.
In the age of ‘hurry up and get it done’ simply replacing a brake drum and shoes is not an effective way to maximize brake life, safety and productivity. Nor is it the best way to avoid costly violations and irate drivers.
“This is the second time they’ve done this to me,” said a driver recently to a Florida Highway Patrol trooper who grounded his truck for bad brakes.
The ‘they’ in this case would be the fleet that failed to ensure that the driver’s trailer had sound brakes before hitting the road. But the driver also shares responsibility since the trailer should pass his own inspection prior to hauling.
The grounded truck and its driver sat and waited at an inspection station along Interstate 10 for a tech to show up to fix the brakes. Both were still there when the trooper’s shift ended, and with a load that was going nowhere fast.
Avoiding violations not only comes from keeping brakes in adjustment it also comes from taking a close look at brake drums, which can reveal how the overall system is performing. Tossing out a drum without closely inspecting it for wear patterns and damage may mean missing vital clues that can point to issues with hardware, shoes and the smallest of road hazards like dirt and sand.
“Any irregular wear patterns should be investigated, such as tapered wear across the braking surface or significant grooving beyond the specific drum’s maximum wear diameter,” says Johnathon Capps, vice-president of engineering, Webb Wheel Products. “Causes for this include worn braking hardware (such as the rollers and bushings), dirt and debris infiltration across the braking surface, and inadequate friction material.”
Accuride’s director of wheel end product engineering, Greg Sturdy, says on average fleets are not conducting enough brake drum inspections. For guidance, Sturdy points to the following recommended practices from the American Trucking Associations’ Technology & Maintenance Council (TMC): TMC RP608 on Brake Drums and Rotors; RP627 Brake Lining Structural Defects; and RP 629 Brake Lining Contamination.
“Even wear is critical,” Sturdy says. “If there is any sign of uneven wear or heat discoloration this indicates the system is not running true to the axis of rotation and causing runout. Such runout will cause the brake components to unevenly heat and cool and cause accelerated wear along with crack formation potential.”
Sturdy adds that grooving can also be caused by aggressive linings, improper brake setup and improper burnishing.
Since brakes are only as good as their hardware be sure to take a close look when the drum is removed.
“Look for damage to components, cracks loose or missing fasteners, corrosion, etc.,” Capps says. “Refer to the manufacturer’s maintenance manuals for specific dimensional inspection points. Also refer to the manual to determine where to lubricate and where not to lubricate.”
Pfost says that while grooving can be caused by foreign material like sand and dirt entering the drum it also may be the result of excessively hard brake shoes.
Picking high-quality shoes to match the duty cycle can help avoid trouble down the road.
“If the drum is wearing faster than expected, then there may be a friction couple incompatibility or that particular wheel end is doing more work than other wheel ends,” says Joseph Kay director of brake engineering, Meritor.
Wear patterns like grooving, however, aren’t always indicative of a problem.
“A groove on the outer edge of the drum is quite common as the drum is typically slightly larger in width than the shoe,” says Mike Hasinec, vice president of maintenance, Penske Truck Leasing. “Deep grooves throughout the drum surface typically indicate the brake lining has worn down to the rivets. Pitting can be an indication of debris getting in the drum — backing plates help prevent that. Some very small cracks inside the drum surface are normal. In rare cases, you may see the drum worn more towards the outside versus the inside. An alignment problem or even a bent or twisted brake spider can cause this.”
The heat is on
Since it takes plenty of friction to slow down an 80,000-lb. truck it’s not hard imagining how hot brakes can get and the impact that heat can have on drums.
“The main function of a brake drum or rotor is to convert energy to achieve a vehicle deceleration,” Kay says. “The drum does this by converting the rubbing friction into thermal energy (heat) and then release the thermal energy to the atmosphere. The drum must have excellent material properties to manage the energy quickly and efficiently.
“For example, an emergency stop with a fully-loaded commercial truck from 60 mph will happen under six seconds, therefore if the energy cannot convert quickly the result will be a longer stopping distance.”
Obviously, no one wants a longer stopping distance, which is a vital reminder of the importance of choosing the right brake components and conducting routine and thorough inspections that include looking for signs of overheating.
“The drum has to handle a lot of variation in temperature,” Hasinec says. “During braking the drum experiences expansion and contraction, which causes many of the smaller cracks you see on the inner drum surface. These smaller cracks are generated from the heat of the braking event and are normal. A lot of heat and a panic stop usually causes larger cracks that can actually be seen from the outer edge of the drum. This is a drum that you discard, as it is usually cracked all the way to the outer shell.”
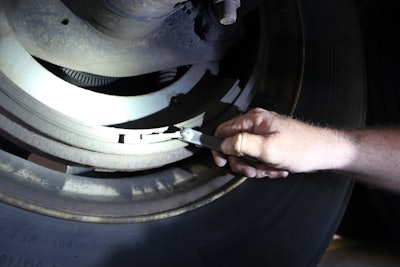
According to Pfost other factors also can lead to abnormal heat in the drum, such as a dragging brake and a duty cycle that’s too severe for the drum. Capps agrees.
“While cracks across the braking surface can be caused from improper installation, it is typically due to a thermal or mechanical overloading of the braking surface,” he says. “This can be due to various factors including: improper installation; inferior friction material; dragging brake, inadequate drum for the specific application; or parking brakes set while drum is overheated.”
While mostly normal, there are times, according to Kay, when those small heat cracks may be signaling a problem.
“With heat checks it’s okay to continue using the drum as they sometimes wear off over time or they do not grow,” Kay says. “It is important to note that heat checks would be expected to cover the drum 360 degrees and over the width of the shoe contact. This symptom indicates the shoe is in full contact when the brake is applied.
“If the drum shows localized heat checking, for example in a certain section of the drum, then there may be a dimensional problem that is forcing contact in only one location,” he continues. “Sometimes the thermal stress will continue fatiguing the drum and larger cracks will develop. Once a larger crack forms then the drum must be replaced.”
Beyond heat cracks look for drum discoloration as a sign of overheating.
“If the brake surface has a blue color to it, this is typically a symptom of overheating,” Kay says. “Dragging brakes or simply over-using a brake can lead to excessive temperatures and as a result the drum turns blue from the oxidation.”
Drum discoloration from heat damage may also result from martensite formation which leads to leopard spotting, Sturdy adds.
Beating the drum about best practices
Since it’s typically more time- and cost-effective to replace old drums with new ones, most shops have largely abandoned the process of turning drums. Penske, however, never took up the practice.
“We have never turned drums and don’t see this as cost effective,” Hasinec says. “Turning drums creates additional down time for the vehicle. Turning drums has become somewhat rare and even finding a supplier that can do so can be a challenge. I believe most fleets have this same train of thought.”
Pfost agrees.
“The down time required to send a drum to be turned can be costly,” he says. “And if a drum is turned too far, it may still be in spec but by the time you wear out a new pair of shoes, it will no longer be in spec.”
“With the skills required to properly setup and align a brake drum on the pilot and mounting flange we are finding more shops are opting for replacement vs. turning,” he says. “Some sites that have consistent and proper maintenance programs we find them utilizing drums without having them turned, merely going from first lining to the second.”
For those times when turning makes sense be sure to take the time to determine if the drum is a sound candidate.
“Most manufacturers do not recommend resurfacing or turning a brake drum,” Capps says. “However, if turning is necessary, allow for at least .040 inches under the maximum diameter cast into the brake drum. For example, if the maximum diameter cast into the drum is 16.620 in., the maximum rebore limit should be 16.580 in.”
When considering a drum for turning, be sure to select proper measurement points.
“This should be measured at the worst location (any grooves or out of round for instance) to make sure sufficient material is there to remove,” Sturdy says. “Check the diameter of the braking surface at two points 90 degrees apart at the inner brake surface area and two on the outer brake surface to check for any roundness or taper issues. Checking in these four locations will help verify the drum diameter as well as any shape issues in the braking zone.”
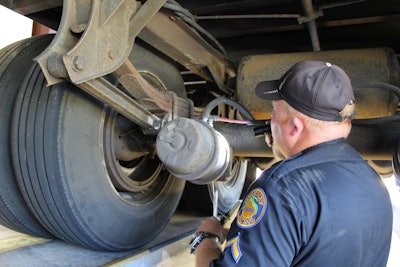
Experts also note to be careful about the turning process, otherwise the drum may be damaged.
“When the drum is installed on the hub it is very important to make sure the run-out is within industry standards,” Kay says. “The objective is to have no run-out. Run-out can lead to reduced brake performance, component damage, and Vehicle Noise Vibration Harshness (NVH), which is irritating to the operator.
“The drum surface needs to be smooth,” he adds. “A rough surface can lead to reduced brake performance. If the machining lead is too large it will cause the brake shoe to move axially causing popping noise. It’s like a record player following the groove on a record. When the shoe gets to a hard contact point it jumps back to center and it makes a loud popping noise.”
Improper turning techniques aren’t the only problem with drum turning. Just keeping up with drum specs can be a challenge.
“The problem I find is that most techs do not know at what measurement the drum is no longer usable,” Pfost says. “But techs tell me this isn’t something they need to know because they replace drums at every friction change.”
With so many training opportunities offered in a range of venues, it’s hard not to stay up on best practices.
Meritor offers free training manuals online at meritorbullpen.com. Training videos are also available along with dozens of courses.
“This is a comprehensive web-based training platform offering more than 100 courses designed to enhance the product knowledge and service needs of technicians, dealer and aftermarket sales professionals, drivers and warranty administrators,” Kay says.
Despite the benefits of improving safety, productivity and avoiding costly violations, training can still be a challenge with some service departments.
“Yes, I think techs understand what a severe out of service drum looks like,” Pfost says. “If they see a crack in the drum — or severe scoring or grooving — it will be changed out. I do question whether they understand the out of service criteria of 0.120-in. over the original drum diameter. I hear from techs that the lip on the drum does not feel too deep. I then share that if the measurement exceeds .060-in. from the top of the lip to surface of the drum, the drum is out of service. Basically, .060-in. is equal to 2/32- or 1/16-in. To make sure they understand this I ask, ‘If they feel a lip on the drum is it or is it not out of service?’ I’m trying to drive home that they cannot tell simply by feeling the lip.”
While best practices in the shop are critical in maintaining healthy brakes, experts adds drivers also can do their part by avoiding certain habits that can lead to premature drum wear.
“Overloading the vehicle, aggressive driving and a lot of hard braking,” Hasinec says. “The wrong friction material for the application can cause this also. Extensive hard braking and panic stops can crack (the drum) all the way to the outer shell and in some cases cause the drum to shatter. Premature wear can actually be normal wear in some cases, due to the duty cycle/application of the vehicle.”