Part choices, maintenance and installation procedures all play important roles in hydraulic performance
When Nelson Jones says every hydraulic system should be well “STAMPED,” he isn’t talking about a label on the hose. The Gates Corporation fleet and hydraulic specialist simply uses the acronym to describe factors that affect performance.
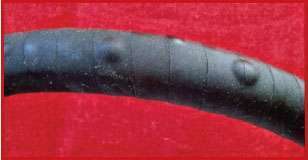
No matter what system is involved, installers and technicians need to consider size, temperature, application, material, pressure, ends and delivery.
Forget any one of these factors and there can be consequences.
The choice of one hose over another offers a perfect example of the way size can affect a hydraulic system. Technicians who replace a hose with a version that has a smaller inside diameter could generate unwanted turbulence in the fluid, he notes. This can cause tubes to swell, cracks to form and pressures to drop.
Discussions about size are not limited to diameter, either. A length of hose in a hydraulic assembly can shorten by as much as four percent when it’s under pressure. “If it’s barely long enough to go from port to port, when it’s pressurized it will shrink a little bit and it actually will pull out of the coupling,” Jones explains.
Taut lengths may not matter as much when working with the lower pressures of a transmission cooler or hot oil line, but they will present challenges when working with the higher pressures that come with a power steering pump.
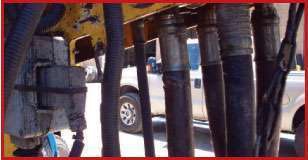
“You always want to make sure there’s significant slack in the hose. You don’t want it sloppy, but you do want to build in sufficient slack to allow for changes to the pressurization,” he says.
When selecting a hose you will need to consider the demands of rising temperatures as well. The life of a hose can be slashed in half if the temperature reaches as little as 18°F above its maximum rating, Jones says. Every hose that looks shiny, glazed or blackened has likely been exposed to that unwanted heat.
For their part, suppliers have found several ways to address the higher heats generated by equipment such as the exhaust gas recirculation system found under the hood of a modern truck.
While traditional TWT (textile-wire-textile) hoses were created to handle temperatures as high as 212°F, options such as CPE (chlorinated polyethylene) were introduced to handle temperatures up to 300°F.
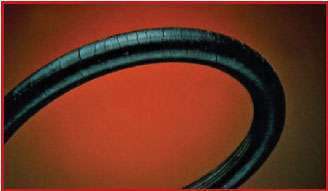
Buyers also can watch for ratings such as SAE J1019, which proves a hose was able to stand up to a 750-hour bath in hot oil — and that can be a key consideration when installing a hot oil lube line.
There are times when the temperature-related support goes beyond the choice of material. The hoses that are mounted near hot components like a manifold or turbocharger may even need the added barrier of a heat guard to protect against constant temperatures that approach 500°F.
Of course, the threats are not limited to temperatures.
The inside of the hose will need to be compatible with fluids that flow through the openings, such as a phosphate-ester or a petroleum-based hydraulic fluid. Otherwise the hose can blister or even disintegrate and create debris that can plug different components found downstream.
Beyond that, the reinforcing layer provides the hose with its muscle, and the cover protects the reinforcing layer from the environment.
The key message here is that every option addresses a specific need.
A typical truck with a diesel engine can include more than 150 ft. of medium- and low-pressure hoses, Gates notes. The low-pressure hose that can handle 200 to 250 psi might work for fuel, oil or coolant lines.
In contrast, a power steering system, fuel filter or transmission coolant line might need a medium-pressure hose (or “flex line”) rated to handle up to 2,000 psi. For their part, high-pressure oil lines tend to include a wire braid, which can withstand higher temperatures.
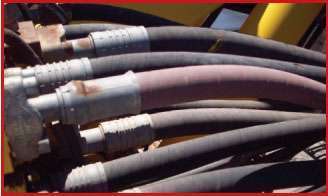
A hose with a braided reinforcement layer will include one or two plies of reinforcement, while a high-impulse hydraulic application might require four- or six-wire spiral reinforcement. Compare that to a suction return hose that would need to rely on a single thick strand of helical wire to keep the hose from collapsing.
Suction, return and pressure hoses are designed for their specific uses, notes Dick Henning, vice president of sales and marketing at BAB Steering Hydraulics Inc. Installing a double wire braid hose as a suction hose will create numerous problems.
A pressure hose (a double wire braid hose) will not fit properly on a suction hose barb (connection) and it cannot be sealed 360 degrees, regardless of the type of hose clamp that is used. In addition, the liner inside a pressure hose is held in place by pressure that is equal at all right angles throughout the system, while the liner in a suction hose is glued in place.
“We encourage people to think in terms of both internal and external factors,” says Jones, referring to hose choices.
“If it’s a pressure line, the fluid is pushing against the walls of the hose trying to get out. If it’s a suction application, the walls of the hose are trying to cave in because there’s a vacuum there. When you’re talking about heat, you want to think in terms of fluid temperature, but also you need to think in terms of ambient temperature. Both are factors today.”
Even though technicians will tend to replace a hose if they see any signs of leaking fluid, they may forget about the leaks in a suction hose that will draw air into the system, Henning says.
Regardless of the hose that is used, installers also need to take care in the way every piece is routed and attached. Every option will have a recommended bend radius. And Jones notes how a seven-degree twist actually can damage the reinforcing layer and shorten the life of a hose by as much as 90 percent.
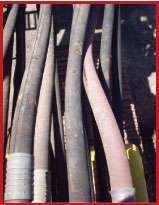
That’s why he always recommends using two wrenches, one to hold a back hex in place while tightening the hex at the very end of the fitting. The printing on the outer layer of the hose should remain straight and true with every turn of the wrench.
The focus on properly securing the hose can’t end there. When diving into dumpsters searching for damaged hoses — to use as examples in training sessions — Jones has found that every discarded assembly shows at least some signs of abrasion that could have been prevented.
Technicians who tie a pressure and return line together, for example, may not think about the way that pressure line will move as it encounters resistance. “People use a nylon sleeve or a poly wrap to bundle hoses together. That’s fine if they’re all pressure lines, but you don’t want to mix return lines in there,” he notes.
The life of a hose also can be shortened by the debris that flows along with the fluid. This is why a system’s filters require some care. “Filtration obviously is important and it can be overlooked,” Jones says.
When it comes to the power steering system, Henning suggests replacing the filter every time the engine is due for an oil change. In addition to trapping dirt, the 25 micron filters are needed to trap the metal removed from the shaft, he explains.
“Once air is in the system, and the air starts to implode, that implosion removes the hard chrome from around the seal surface,” Henning says.
It only takes 25 percent of the implosion’s energy to remove the hard chrome surface from the face of a shaft, and the remaining 75 percent is turned into heat.
Heat is what shrinks the wall thickness of a hose and makes the hose and seals hard and brittle. The more air is ingested, the more hose shrinkage, implosions and removal of the hard chrome surface.
Of course, there are limits to what a filter can accomplish. The debris inside a newly cut hose can do a lot of damage before it even touches the filter mounted by a reservoir. “If it’s a pressure line, that contamination is going to have one good trip down the system before the filter picks it up,” Jones says, referring to the installation work.
Rising pressures are increasing the potential for this damage. Twenty years ago, the typical operating pressures on a backhoe would approach 2,000 psi. Today’s pressures are double that, he adds. “That same level of contamination will cause a lot more damage in a lot shorter time.”
Much of this threat can be eliminated by clearing the newly cut hose of any debris, although the process involves more than a blast of air from a compressor.
Systems such as the Gates MegaClean projectile cleaning system combine the power of shop air, the nozzle for a specific size of hose, and a white foam plug or projectile that will run through the length of the hose to clear out the opening.
The projectile is fired through the hose in both directions before pieces are coupled in place, and sent through one more time after the pieces are connected.
Some makers of major components will void warranties unless the hoses are cleaned with a projectile, Jones adds.
The condition of the fluid is even more important in an era of smaller reservoirs. Power steering reservoirs, for example, once held a gallon of oil. Now they hold about one or two quarts of the fluid, Henning says. That is why he suggests it is important to keep an eye on the color of this liquid. Depending on the formula, unwanted heat will turn the fluid brown or black.
The choice of fluid also will differ from one system to the next. The correct fluid and type is determined by the manufacturer of the steering gear.
Ross does not like to see any synthetics; RH Sheppard systems will recommend synthetic fluids for specific gears. The challenge is that choices often are based on price. “Most people mix and match their fluids, which they shouldn’t,” Henning says, warning against the practice.
The attachments at every end of any hydraulic hose should reflect application-specific needs of their own. Screwed couplings will provide a tight fit with a coupling stem that is screwed into the hose, compressing the hose between the stem and the ferrule.
In contrast, low-pressure hoses can use connectors with stems and barbed ribs. Permanent couplings, meanwhile, are crimped into place.
Indeed, every connection in a system will require specific clamps. A suction hose, for example, needs a clamp that seals 360 degrees around the hose and barb.
A water type hose clamp does not offer a 360-degree seal. “The tang needs to be on the inside to compensate for the worm if you use that type of clamp,” Henning says.
These may all seem like minor considerations, but they can avoid some expensive problems down the road.
“In the steering system, particularly, it could take up to 18 months to see the effects of incorrectly installed or misadjusted gears, poor maintenance procedures, or the use of the wrong fluid, clamps or hoses,” Henning explains, referring to the way problems with a hydraulic system can manifest themselves.
A replaced gear that should last for five years may need to be pulled off the road in half that time. In cases where the original gears only lasted three years because of poor maintenance practices, the wrong hydraulic choices could further shorten the service life to 18 months.
It is simply one example of why it is always important to control the flow.