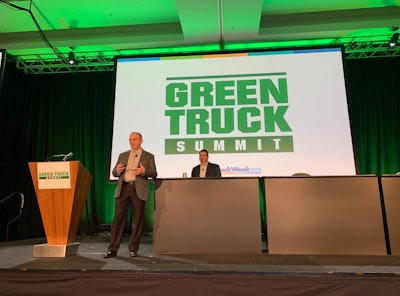
Spec’ing the chassis for an electric truck represents a big departure from diesel and requires closely working with body builders and OEMs to get it right.
During a chassis session Tuesday at Work Truck Show’s Green Truck Summit in Indianapolis, electric truck experts from International Truck talked about the importance of consulting with those in the know prior to making any EV chassis choices. “It is a completely different set of circumstances relative to an internal combustion engine product,” said Bruce Vasbinder, director of International’s medium duty marketing segment.
First up is the battery and its management system. While the battery is housed between the chassis rails, the management system is outside the rails and “needs to breathe” Holland said to help stay cool.
Battery choice incurs quite a bit of the expense in EV selection and also has a big impact on range. It can also take up plenty of space between the frame rails making component placement limited. There’s also the notion of extra weight.
“These vehicles are running 1,800 to 3,000 pounds heavier than the equivalent internal combustion engine product so curb weight is higher, which means by the time you get a body on it, the payload is subsequently reduced,” Vasbinder said.
[RELATED: Barriers to entry for electric work trucks]
Working to recapture some of that payload has been an ongoing goal that’s seeing some impressive results. “We're making the chassis components lighter and we're aggressively working with body builders for components,” Vasbinder said. “We've already worked on a couple of the dry vans and have taken out in excess of 1500 pounds.”
International has worked with Morgan Truck Body and Great Dane to cut weight through material changes and subfloor structure as well as exterior panel structures.
Other factors come into play to help improve overall EV efficiency according to Kevin Holland, International’s director of zero emissions consulting and solutions.
“There's a lot of low hanging fruit, right? And you look at them, the vehicles are heavy so we have to take weight out of vehicles,” Holland said. “We've got to maximize battery packaging design, optimizing the efficiency of the usage of the energy and the batteries through better software. All of that stuff is where we're going.”
Chassis choices in focus
The area on the chassis running from the back of the cab to the axle (CA) is a critical area for a body builder that typically gets more complicated and costly when working with EVs.
“You'll hear the term in truck lingo clean CA, that means keep everything out of bodybuilder's way,” Vasbinder said. “For the end consumer, it means less costs because the bodybuilder doesn't have to move things to accommodate the body that you need on it to do the work you want to do.
“As OEMs we tend to respect that space tremendously. If we have to infringe on it, we try to do it as little as possible. Unfortunately, on electric vehicles we infringe on it little more than we'd like,” Vasbinder continued.
The axle to end of frame (AF) on the chassis also gets plenty of respect.
“There's several different methodologies out there whether you're using an [electric] axle or a pusher motor, like in a bus setup where you have a small prop shaft and a motor that will affect the AF, which again, if you get into certain body applications, makes the body builder adjust the body accordingly,” Vasbinder said.
[RELATED: Cummins CEO talks messy middle of decarbonization]
Electric power take offs, or ePTOs, are another consideration.
“There are a few products on the floor today that are demonstrating [ePTOs]. A year ago we were saying, it's probably two to three years out, but the speed of what is happening in this industry right now is, to me, astounding. I've been doing this 24 years, and I think there's only one thing in the industry maybe moving even close to that and that's ADAS systems,” Vasbinder said.
Fleets have been slowly adopting zero emission vehicles, namely all-electric, particularly in California where the state is implementing a gradual transition to only zero emission truck sales by 2040. Refrigerated trucks are being targeted more aggressively and International has responded by working with body builders to help optimize the transition to all-electric.
“After Dec. 31 of this last year or in calendar year 2023, if you own a refrigerated vehicle or a transport refrigeration unit in the state of California, you have to start working at replacing those vehicles at a 15% rate year over year with the intent of replacing 100% of your fleet by Dec. 31, 2029. That’s a pretty aggressive march,” Vasbinder said.
“And they went after TRUs specifically because typically they just siphon either diesel or the other fossil fuel out of the fuel tank and run the refrigerator units,” Vasbinder continued. “They don't have after treatment systems and they don't have particulate filters so they went very aggressive after the replacement of TRUs.”
Holland said the shift to zero emissions will remain an important focus as the company aims for diesel parity.
“There may be alternate technologies that exist along the way, but we are looking at 10 to 15 years out the internal combustion engine as really not being a primary player for us in the industry. That's where we're going as a manufacturer,” Holland said.