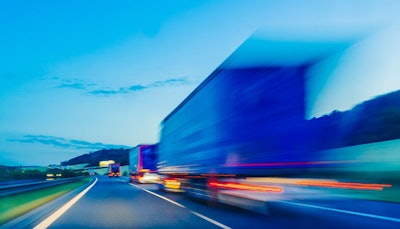
Law enforcement will be paying closer attention to unsafe driving behaviors of both truck and car drivers July 12-18 as part of the CVSA’s Operation Safe Driver Week.
Next week’s push marks the first — and one of the largest — organized enforcement campaigns since the coronavirus pandemic cancelled CVSA’s annual International Roadcheck inspection blitz in early May.
CVSA says less traffic on the roads due to the COVID-19 pandemic may be encouraging some drivers to ignore traffic safety laws, including speed limits. A number of jurisdictions, CVSA says, have seen “a severe spike in speeding” during the pandemic. To combat that trend, CVSA has selected speeding as the focus area for Operation Safe Driver Week — and being pulled over for speeding is an invitation for officers for deeper driver and vehicle inspections.
The special focus on CVSA’s now-postponed Roadcheck was slated to be “driver requirements” — CDLs, medical cards, seat belts, records of duty status, ELD compliance and more – during the 72-hour ramp-up in enforcement.
The CVSA’s decision to focus on driver requirements this year stems from the 2018 implementation of ELDs.
While driver qualifications are the focus of this year’s event, inspectors will still mostly conduct a full 37-point North American Standard Level I inspection during the three-day blitz. During the vehicle portion of the inspection, law enforcement will check brake systems, cargo securement, driveline components, exhaust systems, frames, fuel systems, lights, steering, suspension, tires and more.
The CVSA’s decision to focus on driver requirements this year stems from the 2018 implementation of ELDs and their ongoing goal to not only get drivers more in-tune with using the devices relative to hours of service but to also help them become more diligent in handling documents required at roadside, says CVSA director of roadside inspection program Kerri Wirachowsky, a former Canadian truck inspector.
Last year, more than 12,000 trucks and 2,700 drivers were placed out-of-service (OOS) during the inspection spree. The top OOS violations for drivers during 2019’s Roadcheck were hours of service (1,179 OOS violations, or 37.2 percent of the total), wrong class license (714 OOS violations, or 22.5 percent), and false logs (467 OOS violations, or 14.7 percent). Last year’s three-day CVSA inspection blitz in June resulted in 3,173 out of-service driver conditions.
Brakes consistently top the list of OOS truck violations
While there are plenty of things to look at during a roadside inspection, odds are high that if a truck is placed OOS during May’s CVSA International Roadcheck it’s going to be brake-related.
The numbers really don’t change much year to year. Brake violations in some form accounted for 46 percent of all OOS violations during last year’s three-day blitz in June. Braking systems topped the list at 28 percent of OOS citations and brake adjustment came in No. 3 at 17.1 percent.
While there are plenty of things to look at during a roadside inspection, odds are high that if a truck is placed OOS during May’s CVSA International Roadcheck it’s going to be brake-related.
Homer Hogg, director of technical service at TravelCenters of America, points out a common shop approach to brake maintenance that can lead to costly problems down the road at a time when the industry is up against rising insurance rates, costly litigation and a shaky market brought on by the coronavirus.
“Don’t make the mistake of extending your lubrication intervals too far,” Hogg says. “The tendency is to align chassis lubrication with engine oil drain intervals; however, this can lead to slack adjusters getting dry and not operating properly. Additionally, have your foundation brake parts inspected before the vehicle is lubricated. Worn brake foundation parts will prevent the slack adjusters from maintaining the proper stroke.”
Before hitting the road, drivers can play a vital role in preventing expensive violations by conducting thorough pre-checks. The old adage “an ounce of prevention is worth a pound of cure” definitely comes to mind.
“Drivers should visually inspect brake components during daily walk-arounds, looking for damaged or loose-hanging hoses, air chambers, pushrods, or slack adjusters,” says Keith McComsey, director of marketing and customer solutions at Bendix Spicer Foundation Brake. “Compare the relative position of the slack adjuster (angle) on each axle. If they’re different, it could indicate an out-of-adjustment brake or a broken power spring in the spring brake.”
If time is money, Wirachowsky says fleets stand to benefit from taking the time to teach drivers how to conduct thorough pre- and post-trip inspections. Hogg noted the added pressure of hours of service regulations do not have to detract from effective pre-trip inspections as long as drivers are adequately trained.
“If you talk to most companies, they’ll give their drivers 15 minutes front-end and back-end of the trip to do pre and post-trip inspections. You can do a decent trip inspection in 15 minutes,” Wirachowsky says. “I teach an industry course. A lot of people come to that course and we teach them basically what roadside inspectors do and my biggest thing to industry is just because the guy can drive the truck doesn’t mean he knows what he’s looking at during the pre-trip. So, teaching drivers how to do a pre-trip is as important as teaching them how to drive the truck. And most drivers have not been trained to the extent they need to be.”
Nearly 20 percent of inspected trucks had OOS tire violations last year
Tires and wheels accounted for 3,156 OOS violations during last year’s CVSA International Roadcheck – a whopping 19.3 percent of the 16,347 trucks parked during the three-day enforcement event.
“When it comes to inspections by law enforcement, CSA assigns heavy point penalties for tire issues,” says Jason Miller, national fleet channel sales manager for Cooper Tire. “There are four times as many points against you for a worn-out tire as compared to driving a truck with no door.”
Improper tread depth is one of 10 tire violations that can place a truck out of service immediately.
Improper tread depth is one of 10 tire violations that can place a truck out of service immediately. Marco Rabe, Continental’s head of research and development for commercial vehicle tires, says checking drive and trailer tires for at least 2/32 in. of tread and steer tires for 4/32 in. also provides an opportunity to give the tire a full once-over for pressure and damage.
When tires are worn to 2/32 in., treadwear indicators become flush with the tread elements, making determining minimum depth easy. But Pat Keating, senior manager of field engineering for Yokohama Tire, said any depth greater than 2/32 in. should be measured.
Paul Tatarchuk, B2BN special services coordinator for Michelin North America, says the minimum tread depths set by the U.S. Department of Transportation are just that – the minimum – and that many fleets establish their own internal tread depth rules through their maintenance policy to determine when tires are to be removed and recycled for retreading.
Miller said cutting it close on minimal tread depth can put a driver in a condition where the truck is legal on the way out but OOS on the way back. “Many line-haul truckers run as many as 2,000 miles per week, up to 4,000 miles for teams,” he says.
With steer tires wearing 10,000 miles per 32nd or less, a tire with 1/32 in. or 2/32 in. to spare is likely to drop below the legal limit by the time the truck returns to the terminal, Miller said. “It’s best to calculate those miles in advance to ensure you’re not cutting your tread depth to below legal limits,” he said.
Inflation level isn’t itself an OOS violation unless the tire is legally flat, but overinflation and underinflation are leading contributors toward other citations.
“Thumping a tire with a mallet or club is and always has been useless,” Tatarchuk says. Inflation levels should be checked using only an approved pressure gauge, he said.
“Using a thumper — a tire bat — is a longstanding ritual that really identifies only tires that are dead flat,” Miller says. “A tire that’s 20 percent to 30 percent underinflated is very tough to identify with a thumper.”
Proper pressure not only helps avoid potential violations, it also increases tire life, reduces fuel consumption and improves retreadability, Keating says.
“A $10 stick gauge is worth its weight in gold if used properly and consistently,” he said. “Some dealers provide yard checks as a free service.”
Time-consuming manual inspections actually can be more expensive versus investing in digital tire monitoring solutions says Continental’s Head of Research and Development for Commercial Vehicle Tires Marco Rabe.
“In addition, handheld gauges need to be calibrated frequently to ensure accuracy,” he says. “Even fleets with strong, standardized inspection practices can be deceived by an inaccurate pressure gauge.”
The inside position on a set of duals is more cumbersome to inspect, and, as a result, often get less attention, Miller says.
“Unlike steer tires, a low inner dual is very tough to detect visually,” he says. “Not only does that put the low inner dual in jeopardy, the additional load on the full tire it’s mated to may become fatigued.”
“Remember, an inside tire is there for a reason,” Tatarchuk says. “By design, it takes two tires at that axle end to carry the load. If the one inside is not carrying the load, the other is overloaded, and a dangerous situation may arise.”
In some ways, checking just the outside tire can increase irregular wear, because it increases the likelihood that the pressures won’t match, Keating says. Mismatched air pressure can cause irregular wear and have a negative impact on fuel economy.
When duals are mismatched for inflation, the tire with the lower psi wants to run at a smaller loaded radius, causing it to skip to keep up with the full tire, Miller says.
“Just a 5-psi difference in inflation between duals is the equivalent of one tire having a circumference that is 5/16″ smaller,” he says. “That means during every rotation cycle, the smaller circumference tire must scuff ahead to keep up with the tire with more inflation. These tires rotate around 500 times per mile, so simple math means you’re dragging a tire 13 feet every mile under load.”
Cargo securement was the No. 4 violation last year
Cargo securement issues accounted for 12.2 percent of OOS violations during last year’s Roadcheck — the top truck OOS violation that wasn’t component related and the number four violation overall.
“When you step back and just try to look at the basics, the first thing you’re going to do is make sure the load is safe, stable and immobilized,” says Ralph Abato, president and managing director of Doleco USA.
The 387-page instructor’s manual for the North American Cargo Securement Standard includes a slide presentation, and viewers are reminded of the hazards of not properly securing a load. One image shows a bulldozer that was improperly secured on a trailer with a single 3/8-inch chain. During a hard stop, the dozer launched into the cab and killed the driver. In this case, the choice to not follow a load formula proved deadly. For others, it may result in a costly out-of-service violation during the May blitz.
“The next basic thing is the general requirement for load securement is a formula. And that is you need to double-check the number of tie-downs that you’re using against the weight of the load,” Abato said. “Basically it’s a formula so you have to be at a minimum with the working load of all the tie-downs. Whether they be chains or web straps they need to be one-half aggregate of the weight of the load of the cargo. It’s pretty basic. But if the drivers don’t know those laws, then they’re in for real problems.”
Abato reminds that keeping up with new cargo equipment can lead to safer loads and improved working conditions.
“[Improper load securement] creates workers comp claims [and] damage to the cargo,” he said.
Lights are the easiest roadside violations to spot
While keeping the lights on seems like a fairly easy thing to do, 11.5 percent of last year’s out of service truck violations during the Commercial Vehicle Safety Alliance’s (CVSA) International Roadcheck were caused by light failures.
Unfortunately, fixing outages on the road may entail a lot more than simply replacing a broken bulb.
“In this era of LED lighting, lamp failure may suggest broader systemic issues,” says Optronics director of engineering Kyle O’Dell. “A lamp that appears to simply be burned out turns out to be caused by corrosion in that lamp’s branch of the electrical system. This means moisture is loose in the entire system — and a bigger problem.”
During inspections, O’Dell recommends drivers and techs diagnose light failures by first checking for disconnected, broken and cracked lamps. If connections and lamps are fine, then move on to wire harness segments and connectors closest to the malfunctioning light.
“Many fleet maintenance professionals think of corrosion as a more winter-related issue,” O’Dell says. “However, though brutal cold-weather conditions and chemicals in Northern regions may help to compromise an electrical system, warmer, wetter weather actually amplifies the spread of corrosion. Every 50-degree Fahrenheit rise in temperature doubles the rate of corrosive activity.”