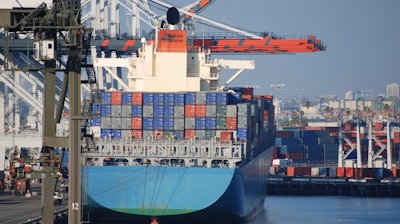
This year, for perhaps the first time, the 'supply chain' has entered the national news. Many average citizens are puzzled, not to mention concerned and sometimes angry, about problems blamed on the 'supply chain.'
Now, many of you reading this have worked as a part of the supply chain for many years, as I have. Even so, it is hard to appreciate the complex dynamics of this system. And how fragile it can sometimes be.
I have had the opportunity to work at several levels of the global supply chain for more than 20 years and have bought hundreds of containers of goods from more than 25 Asian suppliers. I’ve never seen anything like 2021.
I have been studying this for some time now and want to share some things I’ve learned — particularly those that contradict the sound bites on the news. No surprise that the current supply chain crisis is a lot more complex than cable news can report.
[RELATED: The 'everything' shortage facing manufacturers]
First, just a bit of theory. Increased volumes often disrupt complex systems, based on what’s called the 'bullwhip effect.' This is the tendency of complex networks to amplify signals and increase variation. Part of the reason for this is that as a volume change runs through a dynamic supply chain, constraints appear — sometimes in unexpected places.
These can be simple. For example, as volume increases, the presence of stacks of inventoried containers may slow down the flow of other containers. What isn’t at all obvious, or consistent with common sense, that many of these effects are non-linear, even exponential. Thus, as you approach some constraints, the delays can quickly get out of hand. People generally think — and common sense dictates — that things behave in a linear manner. But complex networks often don’t. It turns out the math behind these markets is very complex.
So, a 10 percent increase in volume may result in a 40 percent slower time; a 25 percent increase in volume can bring on a total halt! If you question this, see the note below on some interesting videos available for free on the topic.
Just one example of the impact of a small increase — storage of containers at terminals. Once the normal capacity is reached, further storage can be very inefficient. Consider this view, showing how just five 'extra containers can impede ready access to 16 more properly stored containers:
An example of how just five extra storage containers can impede access to many more containers.
Trade from Asia/Pacific markets to the United States averaged 1.6 million TEUs (20-ft., equivalent container units). The actual increase logged from 2019 to 2020 was 14 percent and 2021 is on target to grow further. That’s an extra 200,000 containers each month!
The two largest Pacific ports in Los Angeles and Long Beach have become the poster children of the supply chain crisis in the U.S. Thankfully, very little UniBond traffic flows through the LA and Long Beach ports. (Most of our goods go further north, using the Vancouver, B.C., Canada port. Recently Vancouver has experienced its own problems due to flooding.)
For general news, though, what is going on in California?
Practical constraints
Some resources in the USA have been short. Some are widespread; others apply primarily to the two large Los Angeles area ports.
- Truck Drivers: Some estimates say the U.S. overall is shorthanded by as many as 80,000 drivers. In our industry we know this all too well.
- Security cleared drivers: To access a port, the driver needs a Federal government background check and is given a Transportation Worker ID Card (TWIC). Besides the general driver shortage, there is a specific shortage of TWIC certified drivers.This has been a nationwide problem.
- Political efforts specifically in California have resulted in changes that if fully implemented will restrict the availability of drivers. This is a new law that requires nearly all truck drivers to be treated as legal employees rather than private contractors. As we know, many drivers own their tractors and sell their services by the job, rather than as salaried employees. The California bill referred to as AB-5 prohibits most truckers from operating as independent private contractors. Technically the law is in effect, but enforcement has been temporarily halted while employers and truckers fight the measure in court. Should the measure survive the court challenge, there will undoubtedly be further decreases in truck drivers in California. (Ironically, this law was passed as a political challenge to Uber and Lyft … who have obtained some kind of exception to the law!)
- Driver choices: These same owner-operators are increasingly choosing other work since their pay for taking a container from the port hasn’t increased but delays have. Some drivers report in the past, they could move five to seven containers a day. Yet now, with current delays, they may be limited to two containers. Understandably, they are choosing better paying work elsewhere.
- Port space for container storage: As delays have increased, most available spaces in and near ports to store containers are full, as noted above.
- Slowdowns due to new COVID-related work rules: As in many other fields, these occasionally add burdens. (A specific issue occurred recently back in China, where one of the major Ningbo container facilities was closed for nearly a month due to COVID quarantine.)
Note that none of these constraints are addressed by increasing the operating hours for the port.
[RELATED: HDMA Pulse Webinar spotlights ports in parts shortage]
Rail congestion
Rail traffic is commonly a major factor in the ocean freight trade. Many containers bound for the Midwest and even East Coast arrive in a California port and are transferred to rail. Rail yards have suffered from similar capacity issues, with container chassis being a particular resource of concern.
These were severe enough in the central U.S. rail hub in Chicago that carriers suspended all service from the West Coast to Chicago for a week during the summer to allow Chicago to improve their backlog. Reportedly, the Union Pacific rail line was backed up with a 25-mile queue of trains awaiting unloading. Chicago freight problems have been accompanied by a major increase in shipping costs.
Unanticipated shocks
Remember how happy we are at UniBond that our goods flow through Vancouver? That was shaken last month when flooding in that area blocked rail lines. As of this writing, that problem is still not corrected, although it’s expected soon. Once again, when there is slack in the system short term problems can be tolerated. But when the system is running full tilt, these problems quickly have a ripple effect.
So, what can a shipper do? If you’re a UniBond direct-ship customer, know we are already doing our level best to manage these problems to the best of our ability.
[RELATED: What OEMs are saying about their order boards]
Elsewhere in your business, here are some of the things we’ve found helpful:
- Be realistic. These problems aren’t going away any time soon. Best guesses are that 2022 will bring more of the same.
- Work with multiple freight forwarders. More options can sometimes help.
- Stay in frequent communication with your forwarder. Like any service, it’s people oriented. Having your forwarder thinking about your business will help. Avoid the natural tendency to vent to the forwarder!
- We also are having more frequent communications with our factories to obtain live updates on shipping activity.
- Be willing to consider unconventional approaches, if the costs are worth it. For example, one of our forwarders discussed using refrigerated containers if they were the only option available, even though our steel auto parts don’t need refrigeration.
(For more insight on the 'bullwhip effect,' consider the following resources. This condition has been known to theorists since the 1960s and studied by accomplished supply chain professionals since the late 1980s. One of the best introductions is a simulation of a simplified supply chain known as 'The Beer Game.' For a quick 10-minute summary, check out this video: https://www.youtube.com/watch?v=1YcYytiE4JA.)