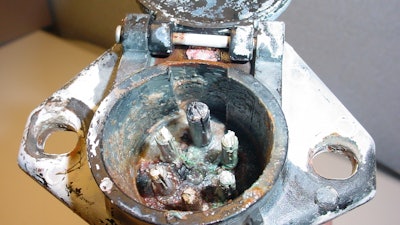
With temperatures falling and cold weather looming, it’s once again time for parts and service operations to prioritize preventive maintenance (PM) programs that can keep customers on the highway during the winter months.
Trucks command a lot of maintenance attention in the winter, and rightfully so, but manufacturers and suppliers say great uptime solutions must cover trailers as well. After all, a sidelined truck can be replaced to keep a load moving and on time. When a trailer is down, so is its cargo, and that impacts everyone.
Electrical systems in particular demand regular attention. All trailers require functional electrical systems to avoid accidents and FMCSA vehicle maintenance violations. Electrical systems also are uniquely vulnerable to the onslaught of moisture, chemicals and other hazards that can make their way onto roadways in winter months.
Corrosion can devastate electrical components and, in winter weather, even the smallest exposed electrical systems can be destroyed by the elements in a matter of days. As Phillips Industries’ Director of National Fleet Sales Andy Summers puts it, “Once moisture penetrates the system, copper sucks it up like a dry sponge.”
Summers references an experiment conducted at Phillips where a wire was placed in a cup of salt water in an ambient setting. Within 24 hours, Summers says the liquid had already wicked its way through to the other side and hints of green were an indication of corrosion.
Clarience Technologies states the same. “Engineers in our Truck-Lite Advanced Transportation Lighting Laboratory have observed corrosion failure within mere hours in simulated conditions. The time it takes for such a failure to happen in the field can range from several hours to days, depending on its severity.”
A close-up image of a corroded wire that was exposed to salt water in a testing environment.Grote Industries
“The chemicals used for snow removal are extremely corrosive to the under carriage of the trailer and all electrical components. The best solution is investing in a well-designed trailer harness system,” says Mark Blackford, Grote’s director of national fleet sales.
Summers adds once deterioration begins, it continues until uncovered and is “likely to create a domino effect throughout the entire system.”
[RELATED: As municipalities adopt alternatives for road deicing, winter parts needs may change]
Stopping corrosion and component degradation should be the goal of any PM process, and a hallmark of any parts distributor’s selling strategy.
Inspections
The first, best defense against trailer electrical issues are regular inspections. East Manufacturing says visual inspections should be conducted on any in-use trailer at least twice per day — pre- and post-trip.
During these inspections, drivers should not only ensure components are operational but also seek to identify if any components appear excessively worn or damaged in a way that could lead to a future breakdown. Any connections or parts exposed to the elements should also be checked to ensure they do not have any openings that could allow water or chemicals into the system.
Wabash Director of Quality and Warranty Eric Farnsworth says, “Physical damage is the most common reason an electrical component fails, followed by inadequate repairs and poor preventative maintenance,” adding a good inspection should “check for damage and validate functionality.”
[RELATED: Trailer orders leapt forward in September]
Trailers should receive even more robust inspections during all maintenance intervals. Summers says Phillips recommends technicians inspect trailers every three to four months, “or sooner for trailers that operate in extreme conditions.”
“Lights should be checked for proper illumination. All connections should be tight. Lighting connections and battery jumpers can become loose from road vibration,” Summers says. “Pin degradation from consistent coupling/uncoupling can also lead to loose connections and poor contact on the seven-way and charging connections at the front of the trailer. All connections should be inspected for signs of corrosion, especially those at the nose.
“Cable jacketing should be inspected for chaffing, cuts or punctures which are forms of entry for corrosion-causing contaminants. Cables that are no longer pliable and hardened in some areas may be hiding corrosion buildup behind their jacketing.”
Blackford agrees, noting the connection from wiring systems to lamps has never been more important.
An incandescent trailer lamp no longer in use. New LED trailer lamps have a longer life cycle than their incandescent predecessors but can still be rendered inoperable when corrosion damages the connection to the LED.Grote Industries
Electrical systems also can be monitored by new technologies. Clarience Technologies states customers can use trailer telematics technologies “to serve as another layer of defense,” and references its Light Out Detection System that enables fleet managers to identify lighting failures remotely while a trailer is in service.
Finally, manufacturers note service providers can strengthen customer bonds by sharing their inspection expertise with customers so they can bolster their in-house inspection efforts.
“Customers who have a vested interest in their operation do their best to inspect and perform routine maintenance. At Phillips, we’ve found a lack of education seems to be the biggest contributing factor to missed areas of wear and damage that need maintenance,” says Summers.
Investment
Customers also can avoid downtime by spec’ing premium electrical components and replacing them with equivalent systems in the aftermarket.
Strong OEM manufacturing standards is one firewall against premature component failures.
Farnsworth says Wabash suppliers are chosen based “on a range of important factors. At a minimum, suppliers must demonstrate they meet or exceed all regulatory requirements and/or industry standards. They perform the testing that shows compliance. We confirm these components function properly after installation with end of line testing.”
Customers willing to invest in telematics solutions such as Road Ready powered by Fus1on from Clarience Technologies are able to monitor the health and performance of their trailer lighting systems in real time.Clarience Technologies
Blackford says, “Inferior systems will be a constant battle and need constant attention.”
“Spec’ing sealed harnesses and weather-resistant products are a great start,” adds Summers. “Ensuring all components are installed properly, and then finding the sweet spot for routine preventative maintenance intervals for their operation will help alleviate the frequency of downtime. Some require more attention based on the environments they operate in, while others may operate in more favorable conditions for prolonged longevity of the electrical system.”
There’s also the matter of replacing the right part when the time comes. That’s where trusted parts and service providers can really showcase their value. Partners who understand how trailer electrical systems operate and can identify actual root causes to component failures to ensure a single downtime event doesn’t become a recurring problem.
Summers gives the example of a fleet that continues to replace seven-way cables due to trailer lights blinking while going down the road. “Many times, the socket pins are worn or have never been replaced,” he says. “A socket that is five years old with worn-out pins could be the root cause of the entire issue. Replacing cables versus sockets is a costly proposition.”
Farnsworth adds Wabash also requests feedback from customers that have lingering electrical issues, as “providing feedback to OEMs enables them to improve on these systems in the future.”