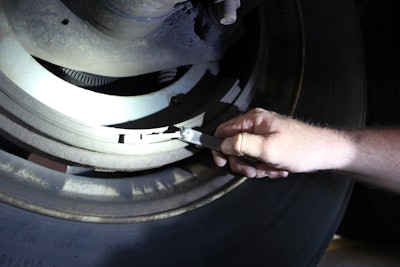
[This article was originally published in 2007 by Trucks, Parts, Service. It has been updated to include more timely information.]
Drivers rely on their brakes to stop their vehicle every time they depress the brake pedal, hundreds of times per day. Therefore, regular inspection of the braking system should be part of any preventive maintenance program.
Things such as routes traveled, duty cycles and braking system types influence how often these inspections need to take place. Webb Wheel Products says a truck being driven out West and in the mountains will use its brakes a lot more than a unit in the Great Plains. And from a duty cycle perspective, wear is more common on the brakes of a garbage truck than on those of a line-haul vehicle, for example, so those brakes would need to be inspected on a more frequent basis.
There's also the matter of reduced stopping distance (RSD) brakes. Accuride states RSD mandates, "while increasing safety for road users, place additional stress on brake system components, making regular inspections even more critical for today’s hard-working commercial vehicles."
When it comes to inspections, drum brake experts say any time wheels are removed from the truck a tech should take off brake drums and perform a visual inspection. Things like a cracked drum are fairly easy to spot during a visual check of the system.
The first step in a proper brake drum inspection is to measure the surface diameter of the drum to ensure it is within specifications.
According to an Gunite maintenance and installation manual for heavy-duty brake drums by Accuride, if the brake surface diameter exceeds the allowable limits, the drum must be replaced.
“The diameter should not exceed .120 in., over the original diameter,” the company manual notes. “When reboring brake drums, the finished diameter should not exceed .080 in., over the original diameter.”
[RELATED: The battle with Rustjacking]
Once you’ve checked the surface diameter of the brake, you need to look for signs of excessive wear or cracks on the brake surface.
“Normal heat checking will occur on the surface of the drum, but you need to look for heat checking that is localized in one area or for discoloration that is localized and not evenly distributed,” Webb Wheel states.
Accuride adds heat checking is “numerous short, fine, hairline cracks on the braking surface of the drum.” It is caused by the heating and cooling of the brake surface, which occurs during normal operation. The Technology & Maintenance Council (TMC) adds heat checking does not impair brake performance and the drum can continue to be used as long as it is within the specified tolerance.
Techs also should be aware that over time heat checks can turn into cracks on the braking surface depending on lining wear rate, braking system balance and how hard the brakes are used.
If the heat checks turn into deep cracks, the brake drum must be replaced immediately.
A cracked drum is one where a crack extends through the entire drum wall. If a tech continues to find cracked drums on a vehicle, it likely means the brake system or brake drum itself are not robust enough for the application or that the vehicle’s driver is abusing the braking system.
Another thing to look for is hard spots on the drum surface. Also known as martensite, experts say these spots are the result of improperly balanced brakes, a dragging brake or an out-of-round drum. What occurs, according to Webb Wheel, is one spot on the drum heats up much more rapidly and more often than the rest of the drum.
[RELATED: Why regular brake inspections are vital to reducing downtime, roadside violations]
According to TMC, martensite forms when brakes are rapidly heated to approximately 1400ºF.
Accuride notes while checking brake drums its also a good idea to check a truck's slack adjusters. "Slack adjuster free stroke measurement is another quick check to help ensure safety of the brake system. Excessive free stroke can indicate issues within the brake system such as excessive wear on the drum or brake shoes," the company says.
By taking these simple steps, service providers and fleet technicians can be assured their vehicles will not be at increased risk for an accident and can avoid being placed out of service by a CVSA roadside inspection during Brake Safety Week or another inspection event.