The hunt for causes of unwanted vehicle vibrations can seem like a game of hide and seek, and a costly version of the game at that. Many technicians attack the issues by replacing one questionable part after the next in the misstaken hope of finding the source.
This was certainly the case for the first 300 trucks that Eaton hooked up to its Driveline Vibration Analyzers (DVA) about five years ago. Technicians had been baffled by the shaking vehicles, which had each averaged about $9,300 in related repairs. But equipped with the modern diagnostic tool, teams identified most of the issues within a day, leading to fixes that averaged little more than $900, plus the identified repair.
“It takes down all the guesswork,” says Eaton Product Service Manager Lon Miller, referring to the value of the diagnostic tool. “I’ve never seen it be wrong.”
And the technology keeps getting better as electronic vibration analyzers continue to evolve.
The attachments that now fit under the driver’s seat give the graph-producing tools an accurate idea of what a driver literally feels in the seat of his pants, measuring individual frequencies that can be matched to specific components from wheel ends to drivelines. One speed channel is simply screwed into the engine’s flywheel housing while a similar attachment sits at the rear of the transmission, working much like a speedometer that tracks a spinning tone wheel.
Anything that focuses the troubleshooting efforts will be a welcome alternative to throwing new parts on a truck until the problem disappears. “We’ve had people install a new engine in the truck and still have the same vibration complaint,” notes Zack Ellison, director of customer technical support at Cummins.
“The OEMs do a much better job today than they did 10 years ago,” he adds, referring to the improvements in the use of mounts and the way these individual components dampen noise, vibration and harshness (NVH). But vibration-related troubleshooting efforts may need to be more refined than ever now that drivers have come to expect more of a car-like ride.
As valuable as diagnostic tools like an electronic vibration analyzer can be, troubleshooting efforts can still benefit from a few pointed questions to the driver, especially in shops where the tools are not available.
“When does it do it? When doesn’t it do it?” asks Charles Allen, director of global customer service at ArvinMeritor, referring to the valuable details about vibration complaints. “Try to be that specific because that can help guide you.”
For example, a vibration that only occurs when the engine is not in gear will eliminate driveline issues, but driveline vibrations will likely emerge at a specific speed and become harsher as the speed increases. In contrast, a vibration that occurs at a specific speed and then disappears when the truck begins to travel more quickly might be traced to problems with a tire or clutch.
If a technician is able to join the customer on a test drive, there should be no question about where the vibration occurs. The added advantage of this clear understanding is that there will be a way for the teams in a shop to ensure that a repair has actually “shut off” an unwanted shake or rattle. That is the ultimate goal.
WHERE IS THE TROUBLE?
Unwanted vibrations can be traced to a host of issues, such as an imbalanced driveline or wheels, overhung transmission or the pulses from the engine itself (after all, the combustion process involves an ongoing series of controlled explosions). Or, a damaged clutch may be unable to dampen the vibrations that emerge whenever an engine hits 1,400 rpm.
Yet one of the most common causes will emerge when someone readjusts an air-ride suspension in the name of a smoother ride. That simple act may soften the ride down the highway, but it can also change the angle of the driveline. And incorrect operating angles can lead to a pile of vibration induced troubles including failed transmission gears, synchronizers, differentials, axles, transmissions, pumps or blowers, and the gears, seals and shafts of a PTO.
The operating angles can be measured with an electronic protractor and fed into the software from the component supplier to determine the best possible settings. In general, operating angles should be set at no more than six degrees, while three degrees is best, says Karl Mayer, ArvinMeritor’s director of product line management – drivelines.
“In the case of inter-axle shaft, and really any system where you have two universal joints, you want to make sure the two angles cancel each other out.” This requires the angles to be within one degree of each other. Left uncorrected, the vehicle could face problems with transmission synchronizer pins, or damage to U-joints – often the No. 4 U-joint found at the output of the forward rear axle on a typical 6×4 tractor.
“Realizing the sensitivity of vibrations and how drivelines may or may not impact that, we’ve actually tightened the specifications of the amount of imbalance we’ll allow in the driveshaft,” Mayer adds. “It’s a much, much tighter specification and we realize that’s going to help.”
Never overlook the easy fixes.
Of course, the physical condition of the parts can make a difference as well. A dented driveshaft tube or a missing weight might throw a driveshaft off balance. Even if this issue is not noticed by the driver, it could still lead to vibration-related damage.
And those who are removing the component have to be careful to reassemble everything in phase. The yokes will normally be in line, but there are situations where an OEM will ask for special phasing, which can be identified by the combination of a straight weld seam but a turned yoke.
A few simple marks will ensure that everything is lined up as it should be, Allen adds.
“If the vehicle OEM has chosen to phase the driveline a certain way…you don’t want to just rely on, ‘I think it goes this way.’”
But the driveshaft may be blamed for vibrations more often than it should. It may be easy to replace, and the part is relatively inexpensive compared to the price of a transmission or rear axle, but it isn’t always the culprit. “You’re always going to be able to find some amount of imbalance,” Allen explains. Even if shops invest the time to “super balance” the component, there may simply be other factors that play a bigger role in an unwanted vibration.
“By far, the majority of vibration issues [over 90 percent] have to do with wheel ends,” Daimler Trucks North America suggests. The solutions to these issues will involve maintaining balance weights, or rebalancing tire and wheel assemblies whenever replacement parts are installed.
“How well they are centered [runout] is also something to pay attention to when mounting new tires,” company representatives adds. “Using or spec’ing centrifuge [balanced] drums helps. Most shops have a way to measure runout so these components are centered within specification.”
UNDER-HOOD CAUSES
Other vibration issues can be traced to the mounts and isolators that are designed specifically to protect trucks, components and drivers from the unwanted shakes.
“Even though these look like simple blocks of rubber, a lot of thought, design and testing goes into a good isolating isolator,” adds Daimler Trucks North America personnel.
It would be difficult to underestimate how important these isolators are. Look at the engine alone. Every combustion event will lead to some torque spikes. That can lead to the vibrations which can wear out main bearings, main journals and crankshafts. Luckily, newer engines have been refined to address these challenges.
“When we build an engine there are certain things we can control in the manufacturing process, and we balance the piston, rod bearing, crankshaft and rotating parts, and we work on how we time or phase the air compression into the engine,” says Cummins’ Ellison. Pistons are machined within a few grams of each other. Even the connecting rods are more precise. “They don’t let the [manufacturing] dies run as long as they once did, so the parts come out very, very close.”
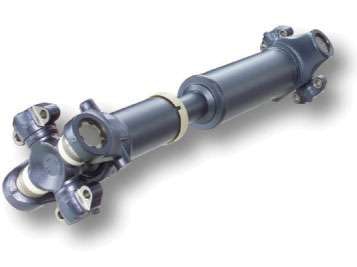
But even when all that is in place, drivers still can begin to report the issues like shaking mirrors that might emerge at low idle speed. That usually can be controlled with engine mounts, as long as the components are working as they should.
A twisted engine mount that allows metal-on-metal contact can present an issue of its own. This “short circuit” can be caused if the frame rails are misaligned, Ellison says. Then the engine’s vibrations will be amplified as they travel into the frame rail.
Installers simply need to be careful about the replacement mounts that they choose. Softer engine mounts may offer a better feel for the driver, but there is a trade-off in terms of shorter component life, notes Mike Bastuk, Cummins’ director of OEM service. The ultimate choice will need to strike a balance between reducing vibration when the engine idles at 600 or 650 rpm and being firm enough to handle the stresses of peak torque.
“The slower the idle speed, the softer the mounts have to be to reduce that natural frequency,” Ellison says. The trade-off is that the life of the mount is sacrificed.
Of course, any of the mounts also will deteriorate over time, and that will happen through the flexing and twisting that comes with day-to-day operation.
Switching drivers can make a vibration magically disappear.
Signs of deteriorating rubber will be easy to see, Ellison says. “You’ll see in some cases where it’s actually melted the rubber…you can see cracks.” But it isn’t always a matter of replacing these parts. Bastuk has seen cases when vibrations have been solved by simply loosening the existing mounts and retightening everything in place, eliminating the dreaded metal-on-metal contact.
It is not the only example of a solution that can be surprisingly simple. A fastener or bracket might simply need to be retightened to hold a component or accessory in place, eliminating a rattle that drivers perceive as a vibration. Recommended torques are also particularly important in the fight against unwanted vibration. “The endplay of the bearing or setting of the bearing may require that nut to be tightened to a certain torque,” Allen says.
Never overlook the easier solutions. Bastuk refers to one situation when a cab began to shake as the truck idled at 600 rpm. He simply decided to reset the speed at 700 rpm and the problem disappeared. “In a lot of cases, if the complaint is at idle, you dial it up 50 rpm and see if that fixes it,” Ellison agrees.
Fleets have even been known to address the problem by assigning a different driver to the cab. Vibrations can be a matter of perception, and the problem identified by one driver might magically “disappear” with the next.
Miller also stresses the importance of a simple preventive maintenance step that can prevent many vibration issues before they occur.
“The best thing you can do is just grease,” says Miller. Even “maintenance-free” drivelines will dry out, and the grease applied to any U-joint should also purge at all four trunions.
There is simply no reason to be shaken by a vibration-related complaint when you’re taking steps like these. n