Tips for troubleshooting (and avoiding) HVAC problems
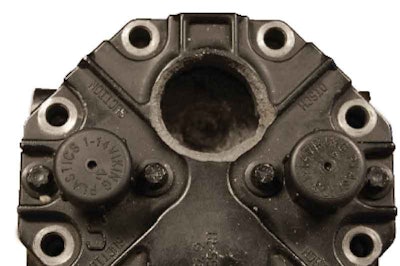
Frank Burrow admits that Red Dot Corporation was mystified when a customer called to report a four-speed blower fan that only worked at a single speed. Every piece of information seemed to suggest everything should work as designed.
Then one member of the team asked whether the cab filter had been replaced.
“Filter?” the customer replied.
The air began to flow as it should once a new filter was in place, and future problems were avoided in the process. “If cab filters are not cleaned on a regular basis, they can cause all kinds of problems,” explains Burrow, Red Dot’s manager of warranty and product support. “This is an area where we can blow up blower motors because of the restriction.”
The situation that was addressed by this manufacturer also demonstrates the importance of asking as many questions as possible when trying to troubleshoot HVAC problems.
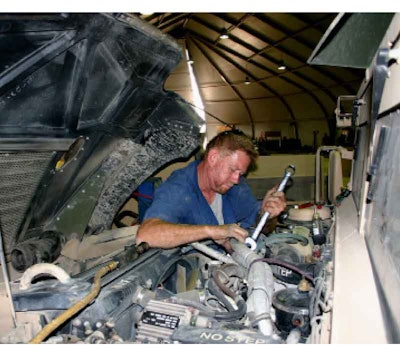
Many of the issues with an HVAC system will only appear when a certain number of factors are combined, so shops need to take the time to record exactly what happened at the time of a failure. If a driver reports that the system stopped cooling, when exactly did it stop? What did the driver do when that happened? Has it happened before? Does he still feel air coming through the vents? Is there any cooling at all?
Equipped with the right details, a shop often will be able to uncover problems that would otherwise go unnoticed.
The potential power issues that might shorten the life of a compressor’s clutch offer a perfect example of some of the problems that could be hiding.
“Clutches on the compressor require a very good ground and a good power feed. As long as we keep the voltage there, we’ve got a clutch that’s going to last as long as the guy owns that piece of equipment,” Burrow says. If there is not enough power, however, the clutch hub will slip against the face of the pulley, generating friction and temperatures that soar above 1,000º F. “It quickly can melt the clutch bearing seal as well as the epoxy compound that seals the coil.”

An initial look may suggest that the clutch is receiving the 11.5 volts of power needed to generate an electromagnetic field, engage the clutch pulley and allow the refrigerant to flow. But it still will be wise to mimic the situations that exist when the system is running outside the shop. “If you’ve got all the lights off and you sit there and take a reading, it may look wonderful. It may look like 12 volts. This guy turns everything on and all of a sudden you’re at 10 volts. Guess what that clutch is doing? It’s slipping because it’s an electromagnet. It depends on that current flow to pull it tight,” he says.
Any attempts to grade the power supply also should reflect the actual installation of the clutch. “If it’s a single wire, the clutch sees its ground on the compressor. Don’t run your ground to the chassis. Don’t run your ground to the motor. Run your ground to the compressor. Duplicate what the clutch is seeing,” Burrow adds.
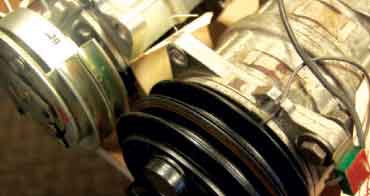
As important as the questions for drivers may be, a well-trained technician also can determine many issues with nothing more than a close look or a careful touch of his own. If a clutch is slipping, for example, the front of the hub also will begin to discolor and the rubber caps can melt. This normally can be seen with the help of a mirror.
The careful looks should not be limited to the clutch, either. Many problems with an HVAC system’s connectors often will be identified by their related oil stains or dirt, while the pink, white or gray dot on a receiver-dryer’s moisture indicator will identify the presence of acid or moisture.
“The second (most important) set of tools you have is your hands,” Burrow says. “If certain components have a lot of ice on them and they’re not supposed to, you’ve got a problem.” The temperature of a receiver-dryer offers a perfect example of the challenges that can be spotted. When it is working as designed, a receiver-dryer will be warm to the touch. Any sign of ice will indicate a restriction in the system.
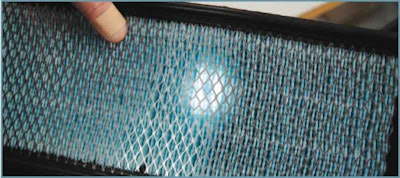
Of course, shops also need to make sure they are not introducing new challenges of their own during any repairs.
A system that is uncapped for too long will open the door for contaminants, and any connections that are put in place need to be sealed properly before the equipment is returned to the road.
As similar as they may appear, there are even differences between one O-ring and the next. Red Dot likes to use HMBR O-rings that will not swell. They also are lubricated just before being installed. “Use virgin product, oil it up, make sure you seat it all the way onto the fitting,” Burrow suggests.
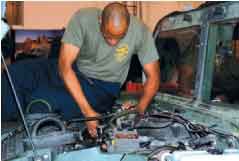
The required torque will vary depending on the fitting, he adds. A Number 6 O-ring fitting will need 11 to 15 ft-lbs of torque, while a Number 8 will require 15 to 20 ft-lbs, a Number 10 will need 21 to 27 ft-lbs and a Number 12 will need 28 to 30 ft-lbs. “We want to make sure they’re not overtorqued — and especially not undertorqued,” he says
One final step also can help to identify potential future problems with any connections. Some anti-tamper tape or even the stroke of a felt pen across two mating parts will make it easier to spot a fitting that has vibrated apart.
And the care of the system’s filters will provide some ongoing protection — as long as everything is clean and properly positioned.
The arrows on a new (or cleaned) filter should be aligned with the desired flow of air. If the filter includes an aluminum mesh that offers some shape and substance, the mesh side should be downstream since it will hold the media in place and keep disintegrating pieces from being sucked into the motor.
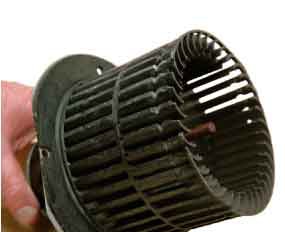
But when cleaning a pleated paper filter, remember to vacuum from the side where the air normally would enter. “You don’t want to suck dirt through the filter. You want to suck it out the way it came in,” Burrow says. Meanwhile, filters made with open-celled foam can be washed with soapy water.
A number of filter designs also will help enhance the overall performance of the system. Charcoal-impregnated filters, for example, can help trap odors, while HEPA filters can trap the tiny particles that would otherwise affect people with allergies or asthma.
As important as different filters can be, however, shops also need to be careful about the compounds they introduce into the systems.
The shelves of most parts stores are lined with one-pound cans of 134a refrigerant, but maintenance teams should be wary about those that are combined with oil and sealant, Burrow suggests. “You don’t know what oil is in there, and every compressor manufacturer today generally uses its own unique blend of oil.” While most compressors use polyalkylene glycol refrigerant oil (better known as PAG oil), others use synthetic ester oil. If the wrong formula is added, the compressor’s warranty can be voided.
Burrow is equally concerned about cans that include sealants. “Sealants look for small openings to plug,” he says. “The system works because it has change-of-state points, and one of those points is at the expansion valve — and it is a very small opening.” The refrigerant will not be able to reach the compressor if the expansion valve is clogged. An exact volume of the material is important, too.
Most compressors are pre-charged with between five and 10 ounces of oil, but there will be a difference from one model to the next. And there is no need to add any oil when installing a new pre-charged compressor. In fact, if too much oil is added, the lubricant actually can form a thermal barrier inside the components.
“Five percent of the volume of gas they’re bringing in will have oil in it,” Burrows says. “If we start increasing that ratio, at some point we’ve got liquid coming into a piston-driven compressor, which generally doesn’t do well.” That’s when reed valves will begin to bend, altering the suction and discharge pressures along the way. Eventually that heat will be transferred to bearings and cause a clutch failure.
Shops obviously need to take every possible step to protect against an HVAC attack.