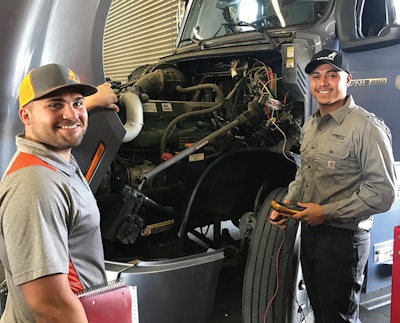
Another important takeaway indicated within Trucks, Parts, Service publisher Randall-Reilly’s 2018 survey of more than 1,200 diesel technicians is the importance of culture in employee retention.
While it might not be a technician’s top priority when hunting for a new job, corporate culture has a definite impact on how long an employee hangs around.
No one wants to work where they’re unhappy.
“Obviously, you have to pay a good wage and provide good health care benefits, but I think everyone knows that,” says Greg Klein, president, Inland Truck Parts and Service (ITP). “I think the other thing that goes together with that is to create a culture where [employees] feel they are a part of something.”
At ITP, Klein says one way that’s done is with the company’s employee stock ownership program (ESOP). Employees gain access to the ESOP during their first year and reap the benefits of the program for as long as they remain employed with the company.
But Klein says ITP’s small tech turnover rate can’t be attributed entirely to the ESOP. He says the company’s commitment to offering a top-rate service experience also helps keep technicians engaged. Between its corporate training center, staffed with four full-time trainers, to its many new, state-of-the-art service facilities, ITP strives to make its service business the vanguard of the independent aftermarket.
“We want to be perceived as a first-class operation and we believe people want to be proud of where they work,” Klein says.
A strong corporate culture can be instilled other ways, too.
A focus on collaboration and positivity has netted a strong service culture for Texas Truck Direct, says Vice President of Operations Christy Cozby.
“Guy [Robertson], who runs our service department, has really pushed a team environment and I think we’ve seen some positive results from that,” Cozby says. “[Sometimes techs] get hot and frustrated and it’s so easy to fall into negative behavior. Guy has really been hitting the shop hard with ‘Let’s have a positive outlook. Let’s treat each other with respect.’ If you can maintain a positive environment, it makes it much easier to come into work every day.”
Ian Johnston agrees.
“Environment really matters. We had a bit of turmoil in our department last year and you could see that wave of morale go down,” says Johnston, vice president, marketing and operations, Harman Heavy Vehicle Specialists.
“It has gone back up again but we could see then how much our culture can impact our employees.”
There’s also the matter of resources. The more a service shop does to provide assistance for its technicians, the less likely those technicians will be to seek out other opportunities.
Klein points to ITP’s training center as an advantage in this area. With each of the company’s trainers offering more than two dozen courses per year, he says ITP technicians have access to some of the best training in the industry at all times. And at a company where every employee’s investment in their work is literally paid back through the ESOP, Klein says most ITP techs are highly motivated to learn and improve their skillset.
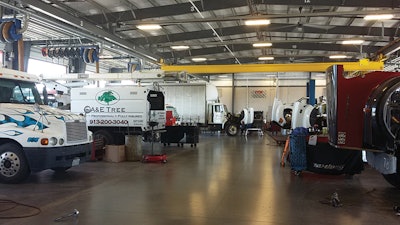
That thirst for knowledge was visible in Randall-Reilly’s survey. Ten percent of heavy truck responders reported continuous education/training or access to the latest technologies as their top motivator when searching for a new job — ahead of location, benefits and even pay.
And these resources and technologies don’t refer solely to training or education. Chris Sterwerf, chief financial officer and chief operating officer, Fairfield Auto & Truck Service, says he’s found success supporting technicians through tool purchases and reimbursements — helping employees cover an out-of-pocket expense most young techs don’t even know is coming until they’ve just begun working in the industry.
“Whether you’re recruiting or trying to keep technicians, you have to do things that make your business attractive. I think something as simple as tools can go a long way,” says Sterwerf. “The cost of tools is a barrier to entry for a lot of young technicians today.”
Sterwerf admits such a move is an investment but says it’s one he’s glad to make to avoid the potential dangers of the status quo.
“I don’t want techs trying to use the wrong tools for the job,” he says. “That just causes more issues for everyone.”
— Online Associate Editor Bill Grabarek contributed to this article.
Click here to download the Randall-Reilly technician wage survey
TARGETING TECHNICIANS, PART 3
Stemming the turnover tide: Investment in your business can help retain your best technicians
Want technicians to stay at your shop? You better pay
Knowledge is power: Technician apprenticeship programs can increase retention rates
Workplace culture can be a technician retention tool
Millennials aren’t from Mars: Generational perceptions impact technician retention