Partner Insights
Information to advance your business from industry suppliers
Distributor of the Year
Keep up to date on the independent aftermarket’s highest honor
Learn how to move your used trucks faster
With unsold used inventory depreciating at a rate of more than 2% monthly, efficient inventory turnover is a must for dealers. Download this eBook to access proven strategies for selling used trucks faster.
Download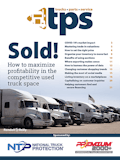
Partner Insights
Products
Parts, components and accessories from OE and aftermarket suppliers
Maintenance
Trucking maintenance how-tos, articles, videos, and more for heavy truck dealers and independent aftermarket professionals on Trucks, Parts, Service.