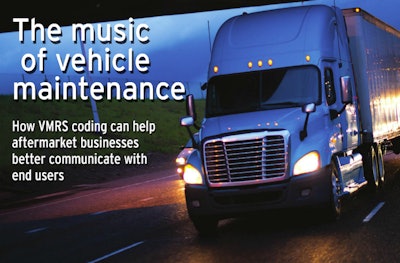
[This article was originally published in 2017 by Trucks, Parts, Service. It has been updated to include more timely information.]
The value of seamless data transfer becomes more evident in the trucking industry every day. From end users to service centers and back; from PDCs out to warehouse distributors; from those distributors to their fleet and service center customers.
Everyone wants to know what’s going on.
While today’s business systems and management software are designed to communicate with each other and share data, trucking’s quest for information precedes the technology being used today to share it. In fact, long before those programs and the internet they rely on came to be, the trucking industry had already developed its own method for sharing data.
Nearly five decades later, that method of Vehicle Maintenance Reporting Standards — VMRS for short — remains as useful and popular as ever. In fact, thanks to its structured design and ability to record any maintenance-related event, VMRS has become more than just a helpful tool to truck owners. It’s a necessity in many of their operations, and one aftermarket partners would be best to note and use.
Some truck owners today aren’t yet demanding VMRS usage by the aftermarket channel, but that future is possible. Rather than wait and risk falling behind, aftermarket businesses can catch up on VMRS today and be prepared for its tidal wave to hit the market down the line.
What is VMRS?
The key to understanding VMRS is recognizing the third letter in its acronym, says Jack Poster, VMRS service manager with the American Trucking Associations (ATA). Poster says VMRS is first and foremost a reporting tool. A standard that can be used across any industry where vehicle maintenance data is recorded and tracked.
The ATA’s Technology & Maintenance Council (TMC), which oversees VMRS, defines the standards as a “structured coding system” that can be used “from total operating systems down to the individual part level.”
Decisiv has published two white papers on VMRS for his customers. In the paper ‘Using VMRS Codes to Unlock Fleet Profitability,’ the company describes VMRS as “an industry standard language that allows everyone in the service supply chain to have a complete understanding of what occurred during a repair, and eliminates the need for extensive written communication.”
Poster likens VMRS to a more famous universal language. “I like to think of it as ‘musical notes for vehicle maintenance,’” he says. “Like music, VMRS is standardized. It’s a language for reporting data that works for everyone.”
[RELATED: Regenerative braking: Catch up on the future of slowing down]
Though it lacks the historical origins of written music, VMRS has been around for many years. Initial conversations regarding the development of a vehicle maintenance reporting language began among fleet maintenance associations in 1969. The first codes were released the following year.
“It wasn’t adopted right away,” Poster says. “It wasn’t until the late 1980s and early 1990s — when a lot of fleet maintenance software forefathers started seeing how the codes and numbers could fit right into their computer systems — when it really took off.”
It is now nearly ubiquitous in the fleet community, and can be found in transportation operations worldwide.
How does VMRS work?
VMRS is built on a structured hierarchy of codes and code keys — hundreds of thousands of two-and three-digit numbers that when recorded in conjunction with other keys (and in specific sequences) provide precise details of vehicle maintenance.
Code keys sit at the top of VMRS’s structure. These keys denote a top-level aspect of maintenance reporting. Riemer writes in his white paper that most code keys fall in four broad categories: assets, service events, repair operations and components.
Within an individual code key there can be hundreds of additional codes that provide specificity and exclusivity related to the original code key.
Poster describes the hierarchy using code key 14, which identifies Reason for Repair. Within this code key are more than two dozen additional two-digit codes categorized into three series of numbers. Individual codes within code key 14 beginning with 0 or 1 refer to reasons for repair related to maintenance. Individual codes in the 20s refer to repair/service work requested by management, and codes in the 30s and 40s relate directly to outside influences, such as accidents, recalls and warranty claims.
For example, a truck entering a bay for a preventive maintenance stop would be recorded 14-08 (code key 14 as Reason for Repair, code 08 as PM). A truck coming in for a breakdown would be tracked as 14-01. A trailer getting aftermarket trailer skirts would be listed as 14-21 (Capital Improvement). The previously discussed warranty work would be 14-37.
Poster says that’s the tip of the VMRS iceberg.
“If it’s part of the service event, there’s a code for it,” he says.
A truck brought in for a breakdown (14-01) can be further recorded using code keys 15 (Work Accomplished) and 18 (Technician Failure Codes), and the specific part descriptor code keys 31 to 34. Regarding code key 18, Poster says it allows a technician to record why they believe a part or system failed. There are 100 two-digit codes within that code key, featuring colorful adjectives such as Battered or Hammered (code 01), Burned, Scorched, Melted or Blistered (02), Warped or Twisted (42) and Noisy (60), to name a few. And those 100 keys are nothing compared to code keys 31 to 33, which combined total “almost 33,000 codes,” Poster says.
[RELATED: Aftermarket service opportunities in preventive maintenance]
These three keys are especially important to aftermarket operators implementing VMRS because they are used to identify parts. Code key 31 refers to a system where a part is found. Code key 32 refers to the part’s specific assembly location. Code key 33 identifies the exact component.
Poster says a front brake drum VMRS codes as 013-001-023. The first three numbers refer to the system (Chassis/Brakes), the middle three for the assembly area (Front), and the latter the actual unit (brake drum).
“It doesn’t matter if it’s a Freightliner Cascadia or a backhoe, 013-001-023 is always a front brake drum,” Poster says.
But whose drum, exactly? That’s where code key 34 steps in. Featuring five-digit codes for all manufacturers and their brands, code key 34 allows a technician to denote a front brake drum from BENDX, STMCO or any other manufacturer.
Where is VMRS used?
Though most independent aftermarket operations are unfamiliar with VMRS, the long-time coding system is visible throughout in the parts and service industry.
VMRS was built into Karmak’s first product when the company entered the market, and the coding system can still be seen in its Legacy product and service software, says John Lebel, strategic partnership director, Karmak. Autopower has a similar VMRS coding chart built into the service features of its products, adds President Mike Mallory.
Some of these features are disabled or hidden depending on distributor preferences, but the occasional dropdown or open forms for codes can be found in both programs.
VMRS’s imprint is especially noticeable for service providers. Decisiv’s cloud-based Service Relationship Management (SRM) platform was designed with VMRS in mind. The platform’s dropdown menus, which allow service providers to record repair actions, parts used and the steps in a service event, are built on VMRS codes.
Michael Riemer, formally with Decisiv, says code keys and code digits are found throughout the platform, typically at the end of menu descriptions.
“We build as much VMRS structure into what we do as we can,” he says. “We’ve implemented it to be completely seamless and transparent. Other than a label or two here and there you wouldn’t even know you’re using it.”
VMRS Code Keys 31 to 33 are slowly filtering into the aftermarket parts world as well. Poster says he’s worked with aftermarket suppliers to slip VMRS coding into their inventories. Some suppliers even include the numbers in their online catalogs.
Lebel says Karmak has started working on an update to its flagship product that will include a swath of VMRS codes. Lebel says the implementation was done at the behest of aftermarket buying groups, who themselves were motivated to use VMRS by their national and regional fleet accounts.
“Their customers are demanding it,” he says.
How does it benefit the aftermarket?
In a competitive aftermarket, VMRS can be a customer service differentiator. With end users becoming increasingly focused on data collection and evaluation to increase performance and profitability, Poster says VMRS allows aftermarket operations to provide concise, easily digestible information customers can add to their in-house records to better manage their assets. VMRS is already in use by a significant majority of CCJ’s Top 250 carriers. It’s loved by government/municipal fleets, relied on heavily in the energy sector, and growing its user base nearly every day.
Poster says that’s the biggest selling point for bringing aftermarket businesses on board. “Your customers are using it and they want you to be using it.”
[RELATED: Why you should consider going online when you're desperate for a part]
He mentions the idea of providing VMRS coding on parts invoices as a way for fleets to easily track what they’re purchasing, and from whom. “You have to think of it from their perspective,” he says.
An order filled with OE-specific part numbers is harder for a customer to read and record. Even in cases where documents are forwarded electronically, a fleet using VMRS is still forced to manually add its orders into its parts inventory using code keys 31 to 34. But if a service provider codes those parts in advance, the data can be seamlessly copied.
Those end-user advantages are even more evident in the service shop.
The “old-fashioned way” of logging a service event by having a technician manually summarize his work is inefficient and not easily replicated, Riemer says. He mentions the example of two technicians at separate facilities providing wildly different descriptions of an identical repair. In that case, the end user must distill the information from both invoices and then use their best judgment to document the work using VMRS in their fleet maintenance system.
Conversely, if those two technicians recorded their work using VMRS, the fleet would immediately see matching number sequences and identify the maintenance was identical.
“VMRS reduces the dependency on detailed technician notes. ‘I found a crimp in the hose and it was damaged so I did this, this and this,’” Riemer says. “There are codes to say all of that.”
“When done right, technicians or shop managers are able to easily assign the codes to the work performed,” says Mallory.
These codes can be used internally by aftermarket businesses as well. The data reported by VMRS isn’t only valuable to an end user.
Parts inventoried using code keys 31 to 34 can be easily examined to determine turn rates; code key 18 is immediately valuable in a service bay when managing a call back; code key 76 (Reason for Delay) is a great way for service shops to evaluate the efficiency of their technicians.
“It gives you benchmarks for everything,” Riemer says.
Poster agrees, adding VMRS provides “true facts you can base decisions on,” as opposed to instincts and anecdotal evidence that can be misleading. “If you’re auditing something you want to have the best data you can.”
How would VMRS be used?
As for implementation, integrating VMRS into an aftermarket business is a challenging process. ATA and software providers (who feature VMRS in their platforms) provide training and guidance to customers who license the codes. Poster says his training isn’t focused on the nearly impossible task of memorizing every code, but instead on understanding how to use VMRS materials to quickly find and select the right code in any situation.
This is especially valuable for service centers, where VMRS codes exist to track every step of a service event. It’s also why Decisiv focuses so intently on automation, with drop-down menus built on VMRS but labeled with general descriptions—such as “Reason for Repair” or “Reason for Delay”—so service centers can use VMRS without requiring extensive technician training.
“[Decisiv] has thousands of users who probably don’t even know they are using VMRS every day,” Riemer says.
Mallory says smart software can make use of specific codes “just a mouse click or two away,” but adds that “educating the end user of the VMRS system and its advantages remains the key to wider acceptance.”
From a parts perspective, VMRS integration requires a lot of up front leg work — adding coding conventions within inventory management software and a warehouse — but once those efforts are complete, “you’re done,” Poster says. He elaborates on that by saying “you only have to add the codes you’re going to use.”
VMRS also covers everything a distributor may stock. Poster says in addition to hard parts, oil and chemicals, code keys 31 to 33 also include shop tools, cleaning supplies and driver accessories. All of which are referenced in ATA’s VMRS training materials.
Though it was built for fleets, it’s clear now VMRS has value for the entire trucking industry. And with customer requests for data at an all-time high, VMRS is a solution the aftermarket shouldn’t overlook.
“It’s a structured language that can work for everybody,” Riemer says. “It doesn’t matter what you are doing and where.”
Adds Lebel, “If you’re trying to share data with someone, you want to know you are [both] speaking the same language.”